This website, introduced in November 2024, uses a new 'IMCA Account' system for authentication.
Previous credentials do not work on this site.
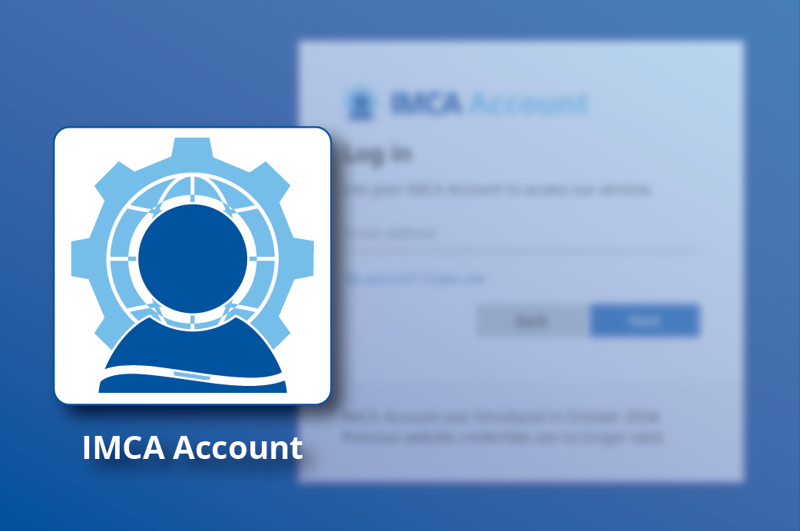
To register for your new IMCA Account:
- Click 'Login with IMCA Account' below
- Choose 'No account? Create one'
- Enter your email address, then click 'Next'
- Check your email (including any junk/spam folder) for a confirmation email
Users working for member companies are automatically recognised, based on registered email domains.
If you need help setting up your IMCA Account, please email it@imca-int.com