LTI: Engineer injured following engine room slip/trip
- Safety Flash
- Published on 27 February 2019
- Generated on 12 July 2025
- IMCA SF 03/19
- 4 minute read
Jump to:
An engineer was injured when he stepped on a loose deck plate.
What happened?
The incident occurred during a dry dock, when an engineer was walking in the engine room searching for a tool and he stepped on a loose floor plate.
The floor plate was not bolted down and slipped sideways. As the plate moved, his leg started falling to the bilge well below, and the opposite end of the plate flipped upwards and struck his abdomen.
He sustained a large laceration to his abdomen which was attended to in the local hospital and required seven days off work to recover.

What went wrong?
There had been a recent overhaul of diesel generators; when completed, floor plates removed to facilitate that overhaul had been replaced but were not screwed down.
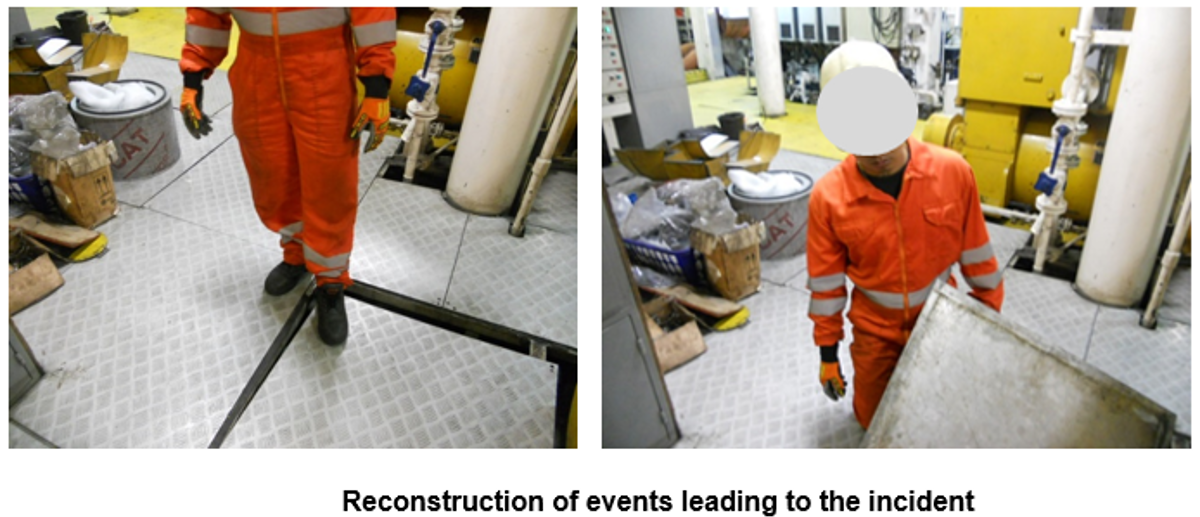
What were the causes?
Contributing causes identified were:
- No stopping mechanisms were fitted on the supporting frames/bars of the plates in order to stop these plates from sliding to the side. One particular plate was bent upwards at one corner and was able to slide freely if not bolted down.
- An existing unsafe condition (the loose floor plate) had been spotted but had not been reported or addressed.
- The permit to work (PTW) closure protocol following the earlier generator maintenance was not followed. No check had been made that the worksite had been returned to safe condition;
Root cause analysis identified that standards, policies and administrative controls were not used effectively – enforcement was not adequate.
- Procedures and overall ethos for safety during the dry dock was not adequate. There had been a failure to properly implement safety in shipyard procedures/guidelines:
- The shipyard safety bridging document had been signed, but was not properly completed and did not effectively bridge between vessel and shipyard safety systems.
- There had been daily morning meetings of supervisors of all parties in attendance, but these meetings had discontinued a week prior to the incident.
- The shipyard safety bridging document had been signed, but was not properly completed and did not effectively bridge between vessel and shipyard safety systems.
- On a day-to-day level, there were gaps in enforcement of the following procedures:
- job safety analysis (JSA) and task planning
- personal protective equipment (PPE) – the injured person was wearing a light t-shirt instead of a full coverall which contributed to the severity of the injury
- hazard observation – the hazard posed by the existing arrangements of the flooring plates in the engine room had not been properly identified
- managing contractors and third-parties – successful integration and supervision of sub-contractor workforce was not applied despite procedures being in place. This led to a loss of control and safety oversight of their activities to some extent as well as a diminishing of the safety culture.
- job safety analysis (JSA) and task planning
Lessons learned
- Attention to detail; personal safety is an individual as well as collective responsibility. In this case, both the unsecured deck plates and IP’s insufficient PPE were noticed but neither concern was raised further or addressed.
- Failure to properly coordinate activities and to supervise the jobs performed by sub-contractors for safe work can lead to serious consequences.
- The shipyard safety bridging document sets the standard for the importance of safety within a shipyard period. The document dictates the involvement of the Technical Superintendent conducting supervision as well as vessel personnel and all contractors involved.
Actions
- Fitted stoppers (flat bars) for plates to prevent recurrence.
- Secured all loose floor plates by bolts.
- Conduct a hazard hunt inspection to identify all similar loose floor plates.
- Modified safety inspection schedule and risk assessment to include checking of floor plates, gratings etc.
- Re-assess high level response to shipyard safety based on IMCA guidance to see if it can be more robust.
Related Safety Flashes
-
IMCA SF 24/17
5 October 2017
-
IMCA Safety Flashes summarise key safety matters and incidents, allowing lessons to be more easily learnt for the benefit of the entire offshore industry.
The effectiveness of the IMCA Safety Flash system depends on the industry sharing information and so avoiding repeat incidents. Incidents are classified according to IOGP's Life Saving Rules.
All information is anonymised or sanitised, as appropriate, and warnings for graphic content included where possible.
IMCA makes every effort to ensure both the accuracy and reliability of the information shared, but is not be liable for any guidance and/or recommendation and/or statement herein contained.
The information contained in this document does not fulfil or replace any individual's or Member's legal, regulatory or other duties or obligations in respect of their operations. Individuals and Members remain solely responsible for the safe, lawful and proper conduct of their operations.
Share your safety incidents with IMCA online. Sign-up to receive Safety Flashes straight to your email.