Crane whip line parted during hook stop testing
- Safety Flash
- Published on 11 February 2021
- Generated on 15 July 2025
- IMCA SF 05/21
- 3 minute read
Jump to:
The crane was positioned in the rest while the Crane Operator carried out hook stop testing of the auxiliary winch.
What happened?
An uncontrolled hoisting movement resulted in the headache ball striking the jib and falling with the hook stop rigging assembly back to deck.
The Crane Operator was testing both the main winch and the auxiliary winch. The main winch was tested and operated normally. When the Crane Operator started to test the auxiliary winch, the winch accelerated to full speed pulling the headache ball into the sheave. The headache ball collided with the jib and the wire snapped, approximately 19 metres from the headache ball. The headache ball (500 kg) and the hook stop rigging (25 kg) dropped 4.2 metres to deck. There were no personnel in the vicinity.
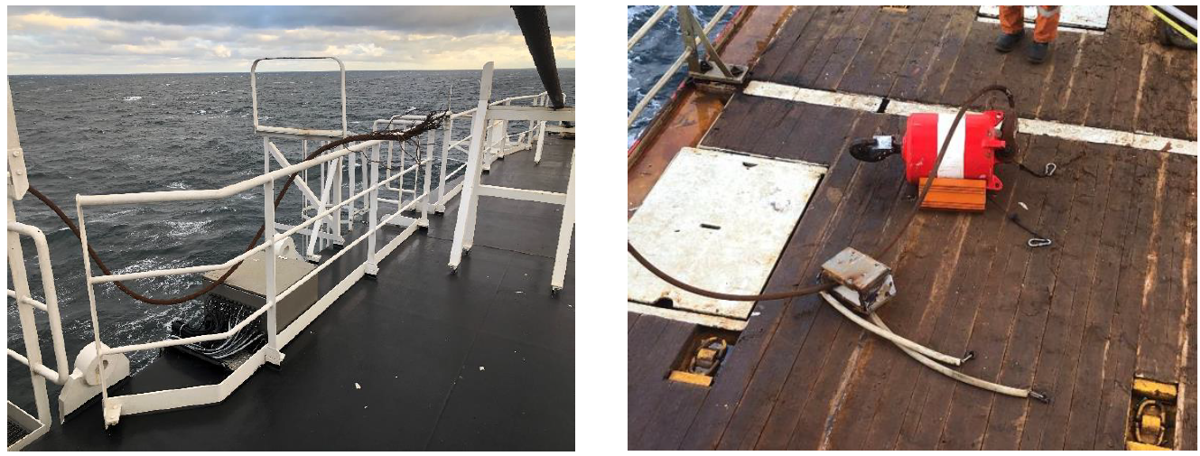
What went wrong?
- The winch was actuated by two hydraulic motors and the speed of the motors measured by encoders. The encoders were badly corroded inside and within the circuit board which resulted in erroneous signal being sent. Both speed encoders required replacement. The crane software was updated to include a second barrier preventing wrong signals from the encoder.
- The winch wire was in poor condition, corroded and dry. The investigation identified deviations from the wire rope management requirements of both the company and the owner of the vessel.
- The auxiliary winch wire was the original wire installed on the winch and had been in service for approximately 7.5 years. Magnetic Rope Tests (MRT) were performed every second year with wire cut-back completed in accordance with the recommendations from the examination. The latest MRT was not completed successfully due to failure in the test equipment and was overdue at the time of the incident. The wire used was 2160 grade which is vulnerable to brittleness; the company does not accept this grade if it is avoidable.
- The risk for using the wire had been identified - however, it was not supported by a Management of Change (MoC) and risk assessment and so no corrective action taken.
Actions
- Check and see if this same encoder component fault can occur on your worksite and check the maintenance routines for encoders.
- Further assure the integrity of wire ropes by carrying out a thorough visual examination combined with either annual Destruction Test or MRT Traces.
- Identify the age of the wire ropes and confirm appropriate in-service reviews have been carried out.
- Ensure formal MoC process is followed where compliance with existing procedures is not possible.
- Review risk assessment for the crane start-up process and ensure that safe positioning of personnel and associated controls are an included control requirement.
Members may wish to review HSS019 Guidelines for lifting operations.
IMCA Safety Flashes summarise key safety matters and incidents, allowing lessons to be more easily learnt for the benefit of the entire offshore industry.
The effectiveness of the IMCA Safety Flash system depends on the industry sharing information and so avoiding repeat incidents. Incidents are classified according to IOGP's Life Saving Rules.
All information is anonymised or sanitised, as appropriate, and warnings for graphic content included where possible.
IMCA makes every effort to ensure both the accuracy and reliability of the information shared, but is not be liable for any guidance and/or recommendation and/or statement herein contained.
The information contained in this document does not fulfil or replace any individual's or Member's legal, regulatory or other duties or obligations in respect of their operations. Individuals and Members remain solely responsible for the safe, lawful and proper conduct of their operations.
Share your safety incidents with IMCA online. Sign-up to receive Safety Flashes straight to your email.