Lost time injury (LTI): Serious foot injury
- Safety Flash
- Published on 9 May 2013
- Generated on 5 July 2025
- IMCA SF 07/13
- 2 minute read
Jump to:
A Member has reported an incident in which a rope access technician suffered a serious injury to one of his toes, leading to partial amputation.
What happened?
During J-lay pipeline operations, a malfunction was discovered in the locking pin designed to lock off the hang-off clamp (HOC). The pin would move down, but not up. Maintenance of the equipment was arranged. A crewman was assigned to clean the hang-off clamp using a water jet, and during this process he was supervised, from the deck level, by the Chief Engineer and 1st Engineer. When the cleaning was complete, he confirmed using hand signals to his supervisors that the job was complete.
The supervising team alerted the crewman that there would shortly be a test movement of the locking pin in order to test the functionality of the equipment. The supervising team alerted the crewman of the imminent movement of the pin, giving signals that he should move to a safer location. He confirmed visually that he had received this signal, but did not move, remaining with his foot on the pin. The 1st Engineer gave instructions via radio that the pin should be moved. Whilst moving, the pin squeezed the toe cap of the crewman’s boot, causing injuries leading to partial amputation of his right big toe.
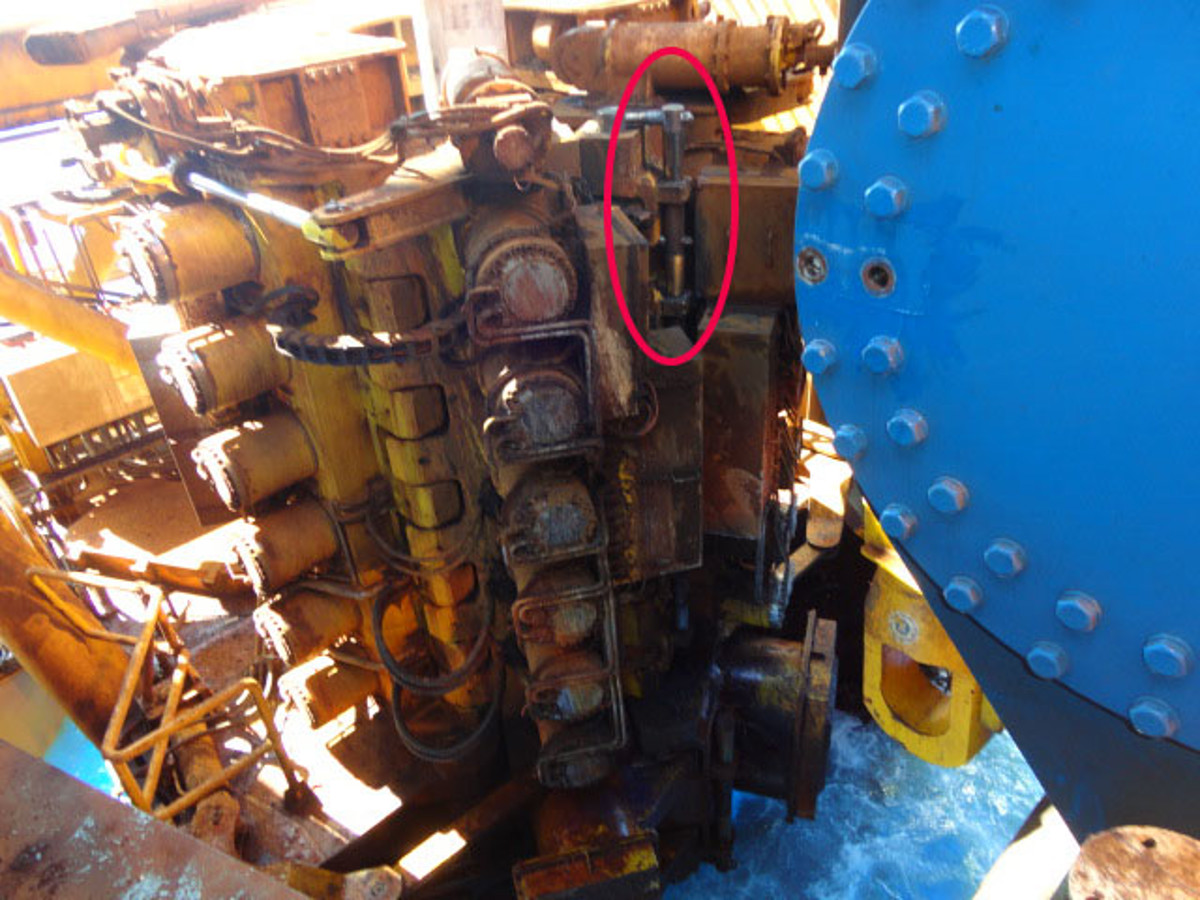
Hang-off clamp locking pin (circled)
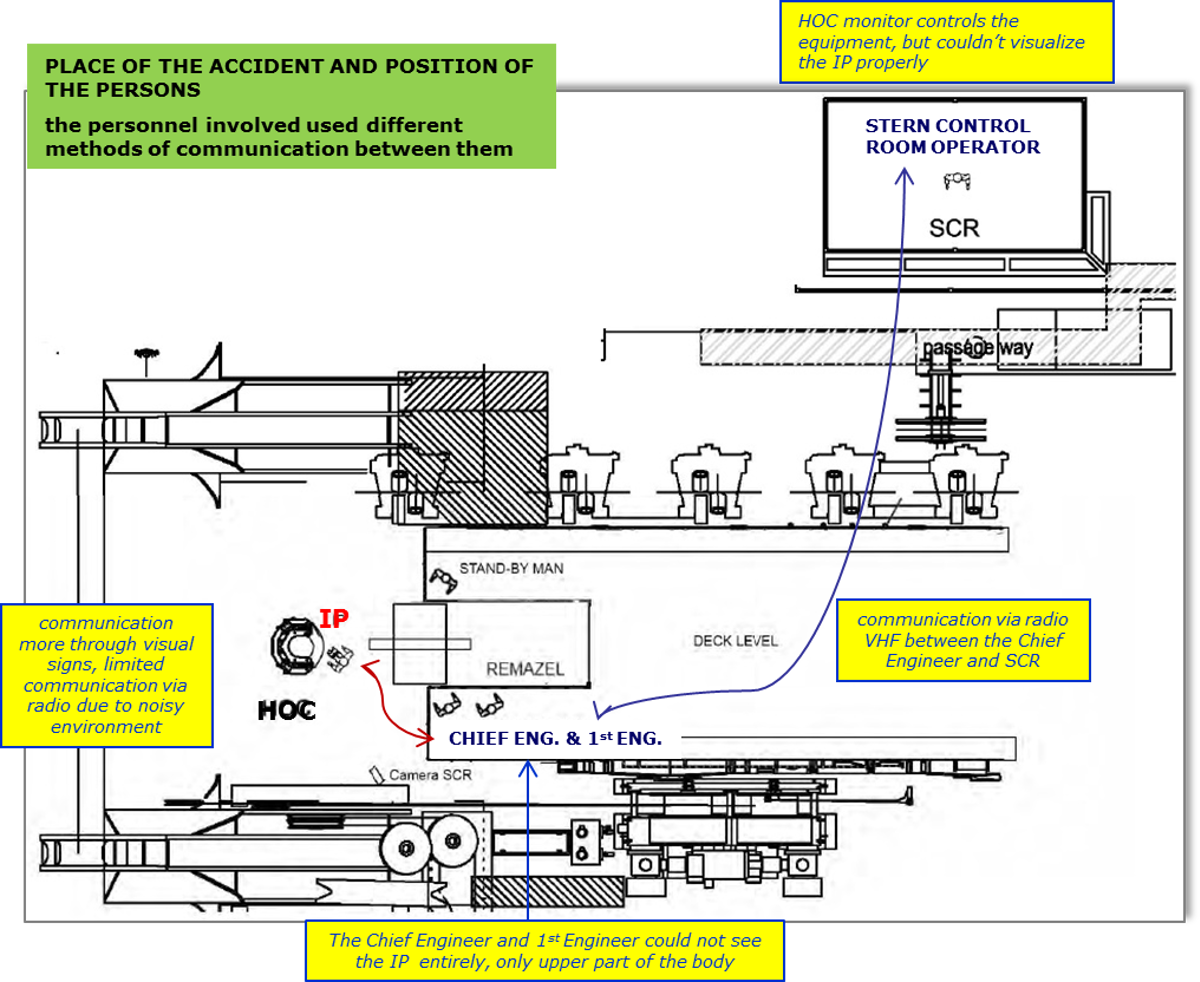
Line drawing showing place of incident and position of persons involved
What were the causes?
An investigation identified the following causes:
- Improper communication between all persons involved:
- Injured person and supervisory team communicated using hand and visual signals and there was no confirmation that the signals were understood as intended.
- 1st engineer and control room operator communicated by radio.
- There was no communication between injured person and control room operator.
- Injured person and supervisory team communicated using hand and visual signals and there was no confirmation that the signals were understood as intended.
- The control room operator could see the hang-off clamp, but could not see personnel working nearby.
- There was no evidence of any toolbox talk before the operation to agree on proper communication channels or planning of the operation.
- Whilst a job safety analysis and permit to work had been issued, these did not fully identify the task hazards.
Actions
The following corrective actions were taken:
- Improved job safety analysis to ensure adequate identification of all hazards and mitigation measures.
- Improved communication protocols and instituted use of common communications channel between crew and control room.
IMCA Safety Flashes summarise key safety matters and incidents, allowing lessons to be more easily learnt for the benefit of the entire offshore industry.
The effectiveness of the IMCA Safety Flash system depends on the industry sharing information and so avoiding repeat incidents. Incidents are classified according to IOGP's Life Saving Rules.
All information is anonymised or sanitised, as appropriate, and warnings for graphic content included where possible.
IMCA makes every effort to ensure both the accuracy and reliability of the information shared, but is not be liable for any guidance and/or recommendation and/or statement herein contained.
The information contained in this document does not fulfil or replace any individual's or Member's legal, regulatory or other duties or obligations in respect of their operations. Individuals and Members remain solely responsible for the safe, lawful and proper conduct of their operations.
Share your safety incidents with IMCA online. Sign-up to receive Safety Flashes straight to your email.