LTI: Contact with refrigerant gas causing hand injury
- Safety Flash
- Published on 12 May 2017
- Generated on 4 July 2025
- IMCA SF 10/17
- 4 minute read
Jump to:
An engineer suffered a freezing burn to his hand when there was a leak of refrigerant gas while he was refilling a vessel’s central air conditioning (AC) system.
What happened?
When the job was completed, the engineer closed the proper valves, disconnected the refrigerant gas bottle, and started the motor to check for any leaks in the system. The AC system was up and running at that time.
But the engineer decided – with the AC compressor running – to give one last torque to the valve to once more ensure it was properly torqued. He crouched and placed himself in front of the point of connection to the hose – “in the line of fire”. Unfortunately, he inadvertently opened the valve instead of tightening it further. It is considered likely that the pin of the ratchet wrench had moved to the opposite position and the engineer did not check the direction of the torque.
There was an immediate refrigerant gas leak towards him. He put his left hand on the leak and tried unsuccessfully to close the valve with the ratchet wrench with his right hand. At that moment, a colleague pushed the engineer out of danger and was able to close the valve in a safe manner.
The engineer’s gloves were initially frozen on; once they were off, his hands were placed in running water. He suffered severe second degree freezing burns to both hands. He was treated on board with the telephone guidance of a doctor, and subsequently transferred ashore for hospital treatment.
It was noted that the client was not made aware of the incident by the contractor until the following morning, and therefore the client (operators) emergency response organisation was not notified nor mobilised. The on-board vessel crew did not immediately realise the severity of the injury and therefore did not communicate it immediately to the client.
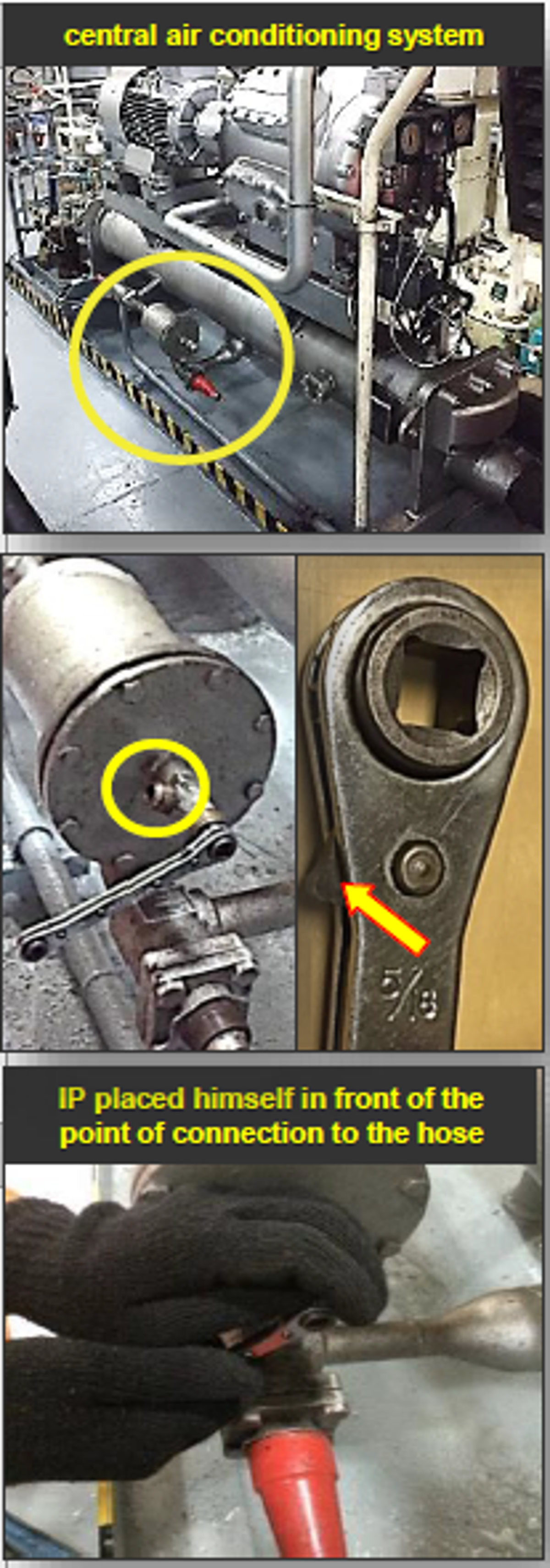
What caused the incident?
Refrigerant gas Freon 404A reaches temperatures of around -46 °C when it is released (i.e. decompressed).
- Lack of risk assessment and proper preparation:
- There was no proper risk assessment nor job safety analysis (JSA) conducted for the task.
- There was no awareness of the dangers involved.
- There was no knowledge of the SDS for this refrigerant gas.
- There was no proper risk assessment nor job safety analysis (JSA) conducted for the task.
- Line of fire:
- The point from which the leak occurred pointed towards the operator.
- The engineer placed himself “in the line of fire” in front of the point of connection to the hose.
- There was improper intervention on ‘live’ equipment without proper safety precautions.
- The point from which the leak occurred pointed towards the operator.
- Procedures:
- The engineer did not check the torque direction of ratchet wrench before use, therefore he torqued the valve in the wrong direction.
- The engineer did not check the torque direction of ratchet wrench before use, therefore he torqued the valve in the wrong direction.
- Personal protective equipment (PPE)
- The engineer was wearing fabric gloves instead of proper thermal protection gloves as recommended in the SDS.
- Thermal protection gloves were not available on board nor had the need for them occurred to the company.
- The engineer was wearing fabric gloves instead of proper thermal protection gloves as recommended in the SDS.
Consequences
- Eleven days in hospital including intravenous medication and surgery to the burnt hands.
- Following discharge from hospital, a further month of physiotherapy before the injured person was fit for work.
Actions
- Proper training in job risk analysis, risk assessment and “line of fire” for crews.
- Permit to work (PTW) to become mandatory for work on high pressure equipment.
- Rotate the position of the discharge point of the compressor so as not to point towards workers, and addition of safety/retention valve (Schrader type valves) on compressor discharge lines.
- Provision of proper and specific thermal protection gloves.
- Reassessment of chemicals used on board and their SDS.
- Ensure that client / operator is informed of any and all injuries on board contractor vessels on hire as soon as possible.
IMCA Safety Flashes summarise key safety matters and incidents, allowing lessons to be more easily learnt for the benefit of the entire offshore industry.
The effectiveness of the IMCA Safety Flash system depends on the industry sharing information and so avoiding repeat incidents. Incidents are classified according to IOGP's Life Saving Rules.
All information is anonymised or sanitised, as appropriate, and warnings for graphic content included where possible.
IMCA makes every effort to ensure both the accuracy and reliability of the information shared, but is not be liable for any guidance and/or recommendation and/or statement herein contained.
The information contained in this document does not fulfil or replace any individual's or Member's legal, regulatory or other duties or obligations in respect of their operations. Individuals and Members remain solely responsible for the safe, lawful and proper conduct of their operations.
Share your safety incidents with IMCA online. Sign-up to receive Safety Flashes straight to your email.