Hot work performed outside of Permit to Work (PTW) boundary limit
- Safety Flash
- Published on 27 November 2024
- Generated on 13 July 2025
- IMCA SF 23/24
- 3 minute read
Jump to:
A near miss occurred when a third-party contractor working onboard a vessel removed a trip hazard (a metal stump section) from the vessel main deck, using a cutting torch and grinding disc.
What happened?
Whilst cutting the 10cm diameter stump, sparks and slag (hot work discharge) dropped into the hole in the deck and fell to a thruster room directly below, onto scaffolding boards and onto a 600V HV electrical cable. There were some burn and scuff marks caused. Vessel engine room crew in the affected area noticed the falling sparks from above, and further identified that there was no fire watcher available in the vicinity. The job was stopped immediately.
What went wrong?
- Less than adequate risk perception:
-
- The third-party contractor failed to perform an assessment of the affected worksite conditions below the deck and did not understand the working conditions in the surrounding area.
- No risk assessment was conducted and as a result there were inadequate controls in place.
- Inadequate communication:
-
- No proper communication was established during the PTW application (it did not include task being performed).
- No permission was sought prior to starting hot work on the trip hazard (stump/cover).
- Assumptions were made that the hot work permit for the welding shop area applied to the surrounding area.
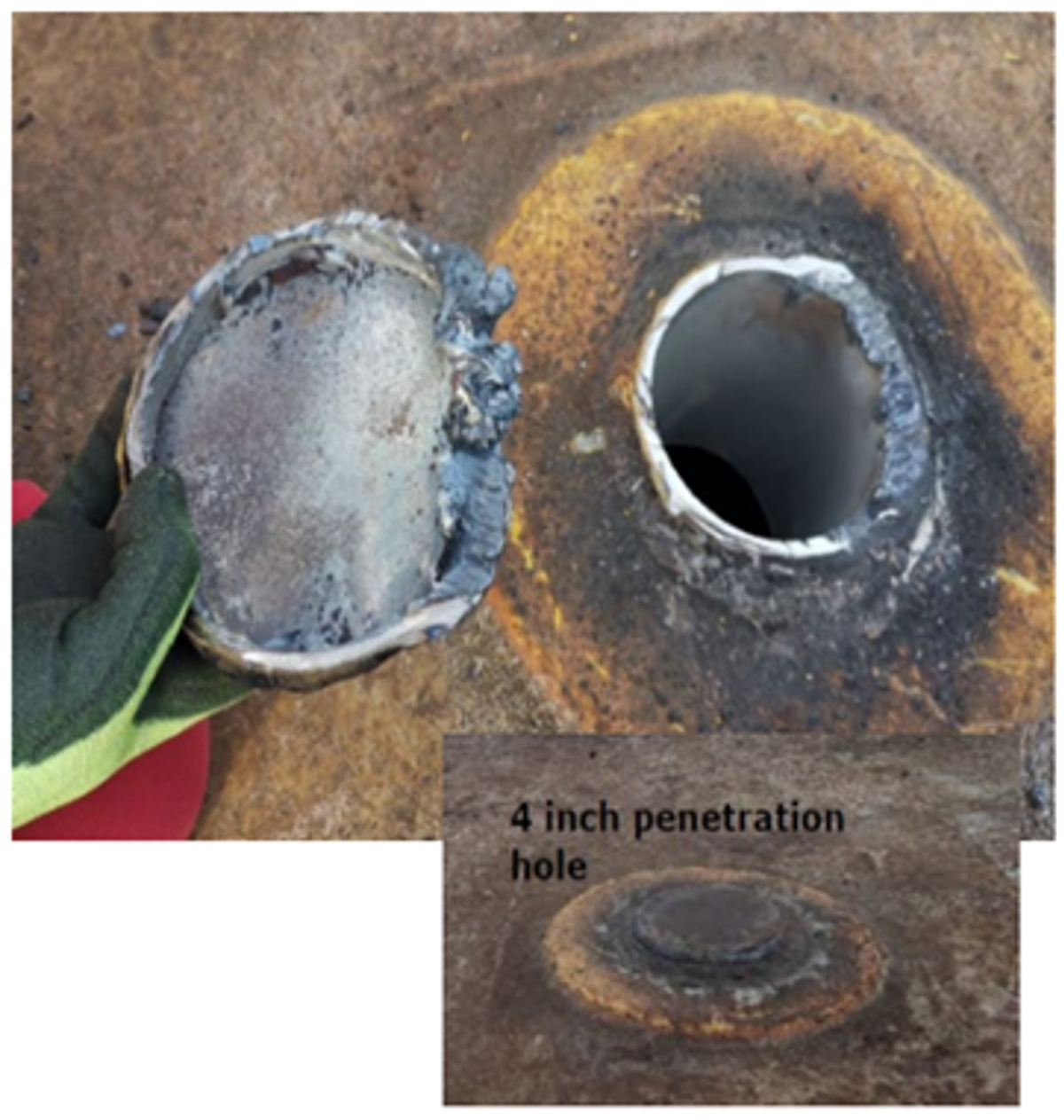
Cut penetration
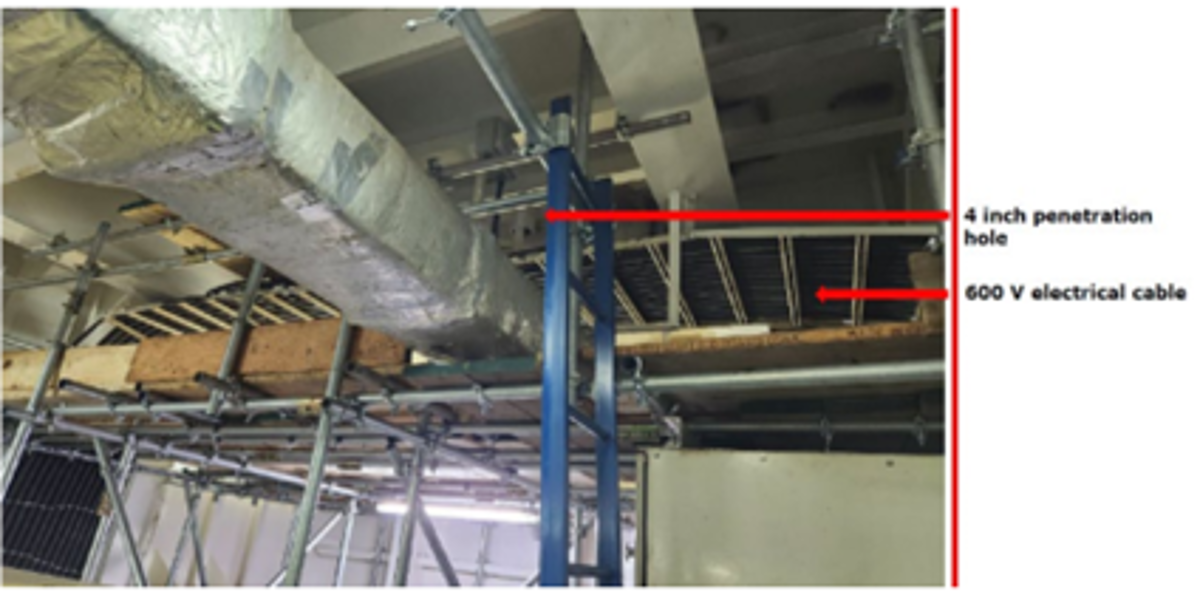
View from area below the deck
- Inadequate pre-job planning: there was no instruction or operational requirement to remove and cut off the stump on the vessel deck. The foreman decided by himself to cut off the stump as he observed that it posed a trip hazard.
- A pre-job site inspection took place at the welding workshop before the PtW was issued but this not did capture what was going on in the deck below.
- Hot work PtW was applied and obtained specifically for hot work activities inside the welding workshop only.
- There was no supervision from any party at the immediate area when the foreman decided to cut-off the stump/cover.
- There was no fire-fighting safety control provided on the deck below.
Actions and recommendations
- Training:
-
- Review and update training material to ensure all aspects of the PTW requirements are captured.
- Ensure third-party contractors receive adequate training (including refresher training) on the Permit to Work system.
- Job preparation:
-
- Review and update pre-job planning, hazard identification, job site inspection and readiness plans before issuing a PTW.
- Ensure all crew involved are properly informed and updated about any Permits to Work in operation.
- Review Task Risk Assessment to capture the lessons learned of the incident.
- Ensure adequate supervision available at site;
- STOP! remind each other that procedures and processes are there to help us.
Related Safety Flashes
-
IMCA SF 06/23
27 February 2023
-
-
IMCA SF 05/22
28 February 2022
-
-
IMCA SF 10/24
22 May 2024
-
IMCA Safety Flashes summarise key safety matters and incidents, allowing lessons to be more easily learnt for the benefit of the entire offshore industry.
The effectiveness of the IMCA Safety Flash system depends on the industry sharing information and so avoiding repeat incidents. Incidents are classified according to IOGP's Life Saving Rules.
All information is anonymised or sanitised, as appropriate, and warnings for graphic content included where possible.
IMCA makes every effort to ensure both the accuracy and reliability of the information shared, but is not be liable for any guidance and/or recommendation and/or statement herein contained.
The information contained in this document does not fulfil or replace any individual's or Member's legal, regulatory or other duties or obligations in respect of their operations. Individuals and Members remain solely responsible for the safe, lawful and proper conduct of their operations.
Share your safety incidents with IMCA online. Sign-up to receive Safety Flashes straight to your email.