Shackle failure during over-boarding of pennant wire and ballast chain
- Safety Flash
- Published on 18 November 2021
- Generated on 12 July 2025
- IMCA SF 31/21
- 3 minute read
Jump to:
During over-boarding of the pennant wire and ballast chain from the main anchor handling winch over the stern roller, there was a failure in the chain link / 35t shackle.
What happened?
The failure occurred and the damaged chain came off the winch, went across the main deck and over the stern of the vessel. Everyone was in a safe position, and no-one was harmed, but there was damage to other nearby winch equipment.
110 m of chain were lost overboard; our Member calculated that this meant there was approximately 31.7t (submerged weight) of tension on the chain at the time of the incident.
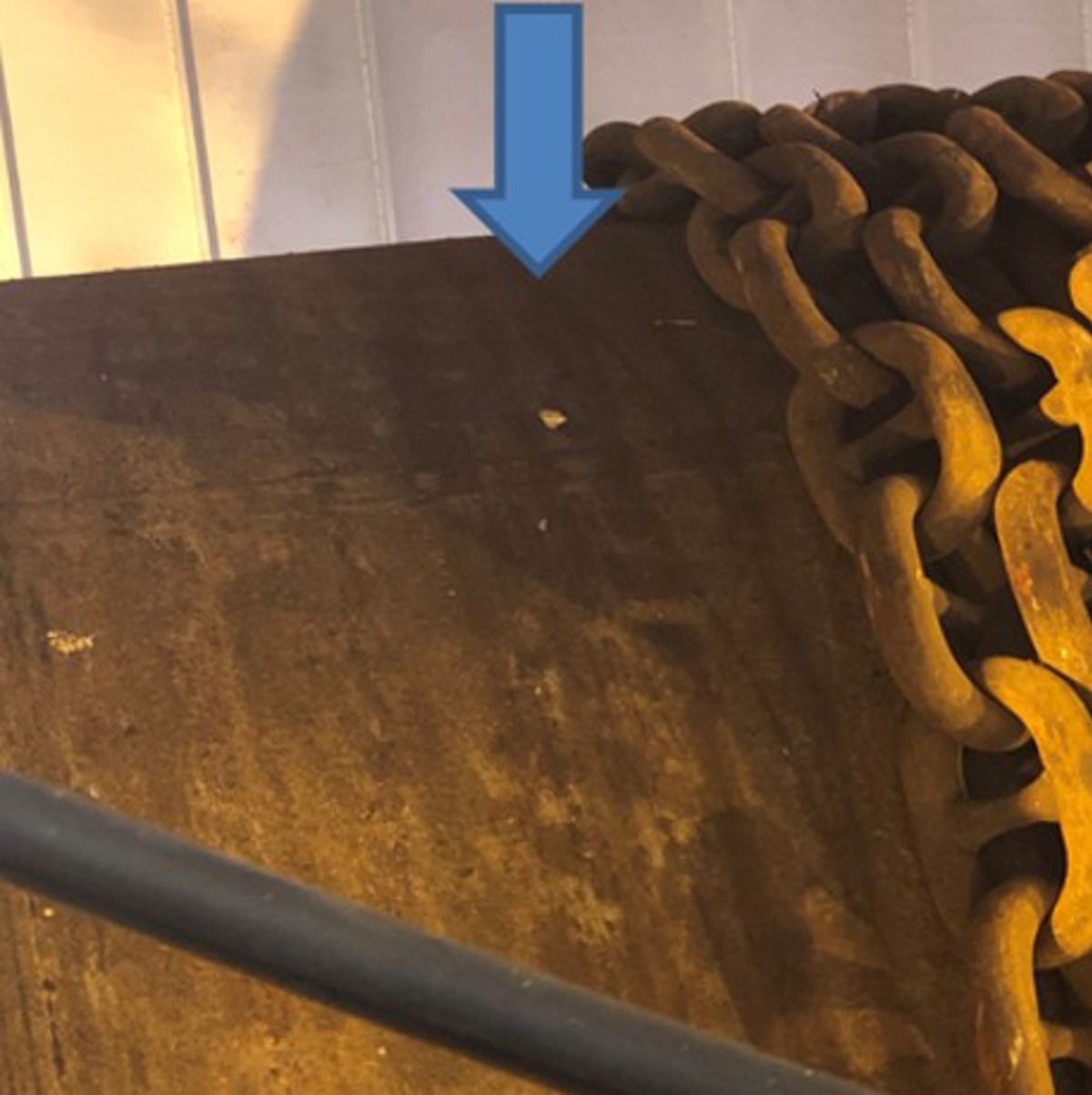
Breaking point location of shackle on drum
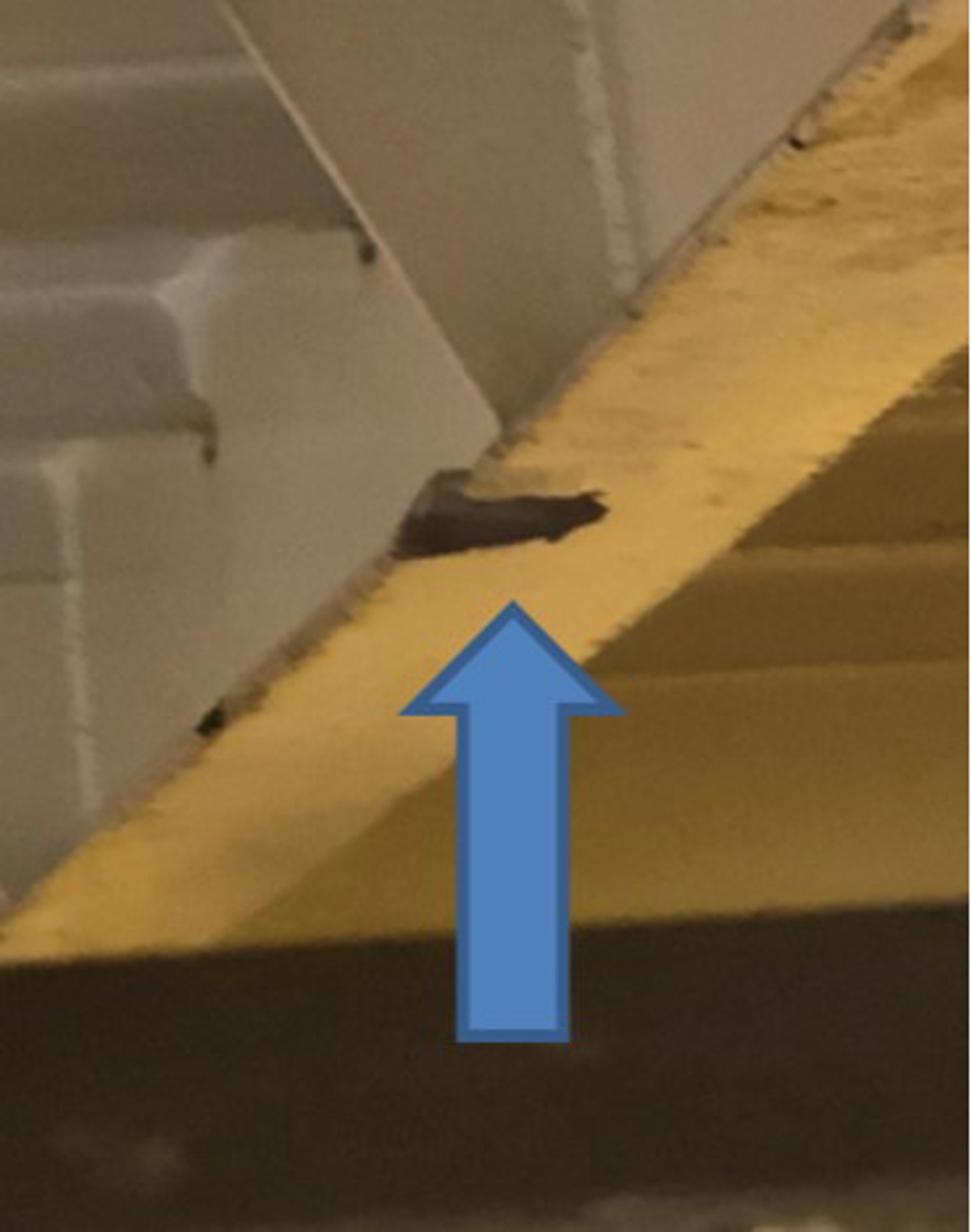
Impact damage from flying chain directly above
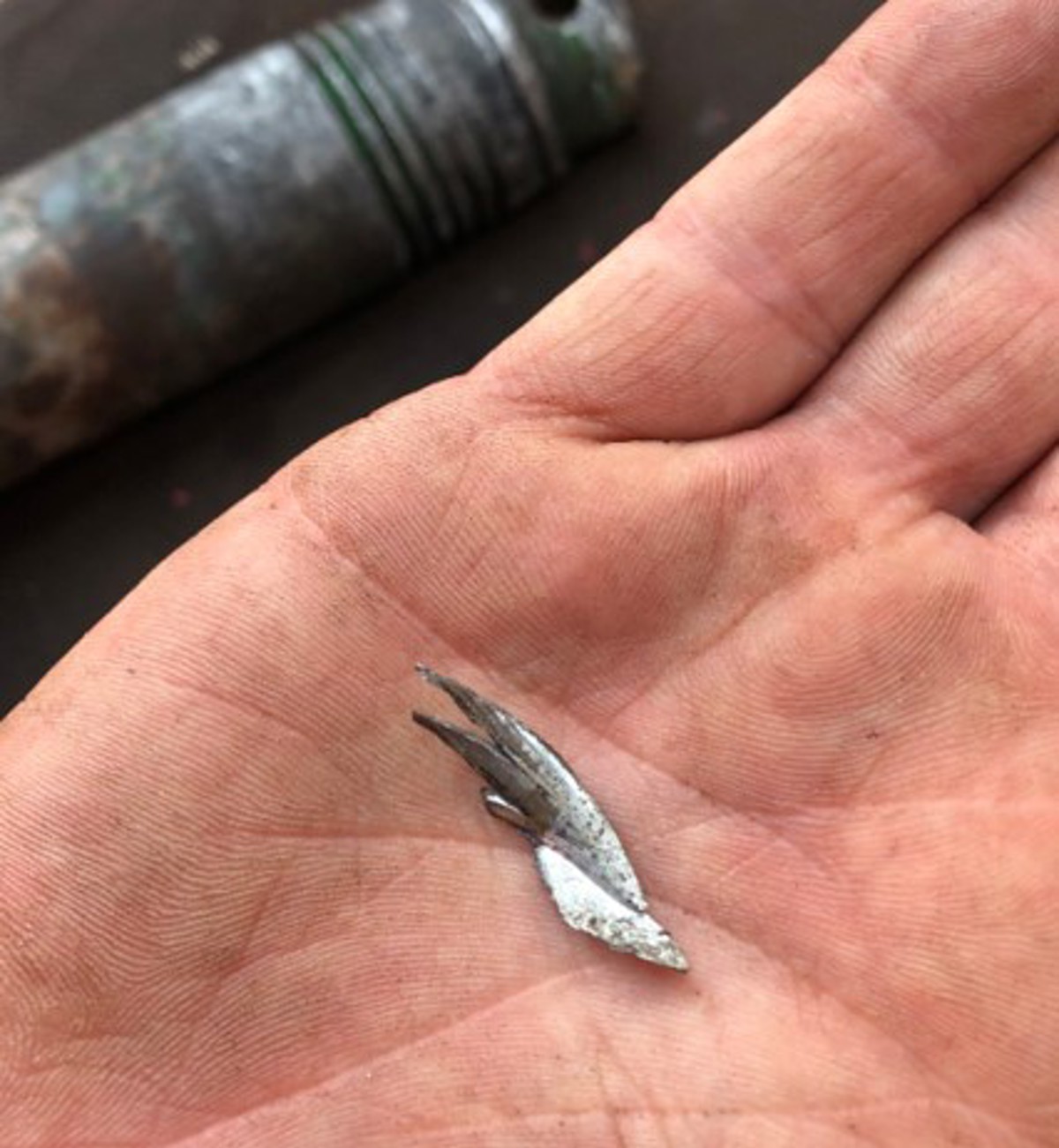
Sheared piece of metal from shackle pin – found close to the winch where the beam was damaged
What went wrong?
- Evidence suggested that during the over-boarding of the chain, the nut on the shackle pin became lodged behind the stud piece of the chain link whilst wrapped on the winch drum.
- When tension was applied on this section of the chain the links straightened and caused the nut of the shackle to be forced off along with the stud piece.
- The resultant shock may have then forced the pin out of the shackle and allowed the chain to part.
- At the point of shackle failure, the chain on the winch drum become loose and whipped towards the special handing winch causing multiple impact damage to surrounding equipment.
What were the causes?
Immediate causes
- Connection of different chain link sections using shackles and spooling them off the stern of the vessel for wet storage.
- The decision to wet store the ballast chain was made onboard and not covered in the original project planning or HIRA.
Underlying causes
- No inspection certificates available for the 82mm chain.
- Poor maintenance of the 82mm chain due to the fact it was only to be used as ballast weight in single 27.5m sections.
- Kenter joining links were not used to connect the section of 82mm chain together, they were ordered but did not arrive.
- Internal signed management of change documentation was missing some important detail regarding the actual connection of the individual chains to be wet stored.
- The chain was connected with 35t shackles which have multiple edges that can be caught or trapped inside other equipment, especially the nuts.
Our Member concluded that that the assessment of risk of connecting the chains using the shackles was overlooked mainly due to last minute change in the engineering planning of this scope of the project (IMCA italics).
Pictures of damaged shackle nut and pin – shackle nut located STB side of winch
near walkway and shackle pin found at the back of the winch.
(Clear indication the shackle was side loaded.)
Related Safety Flashes
-
IMCA SF 25/21
13 September 2021
-
-
IMCA SF 30/19
17 December 2019
-
IMCA SF 21/16
10 August 2016
-
IMCA SF 01/15
16 January 2015
IMCA Safety Flashes summarise key safety matters and incidents, allowing lessons to be more easily learnt for the benefit of the entire offshore industry.
The effectiveness of the IMCA Safety Flash system depends on the industry sharing information and so avoiding repeat incidents. Incidents are classified according to IOGP's Life Saving Rules.
All information is anonymised or sanitised, as appropriate, and warnings for graphic content included where possible.
IMCA makes every effort to ensure both the accuracy and reliability of the information shared, but is not be liable for any guidance and/or recommendation and/or statement herein contained.
The information contained in this document does not fulfil or replace any individual's or Member's legal, regulatory or other duties or obligations in respect of their operations. Individuals and Members remain solely responsible for the safe, lawful and proper conduct of their operations.
Share your safety incidents with IMCA online. Sign-up to receive Safety Flashes straight to your email.