Implosion of chemical tank
- Safety Flash
- Published on 27 March 2024
- Generated on 13 July 2025
- IMCA SF 07/24
- 3 minute read
Jump to:
A chemical tank, partly filled with Monoethylene Glycol (MEG), imploded on the back deck of a vessel.
What happened?
A chemical tank, partly filled with Monoethylene Glycol (MEG), imploded on the back deck of a vessel, resulting in a spillage of around two cubic metres of MEG to the back deck and to sea, and unrepairable damage to the tank itself. There were no injuries. The tank was a 26 cubic metre tank, containing 10 cubic metres of MEG.
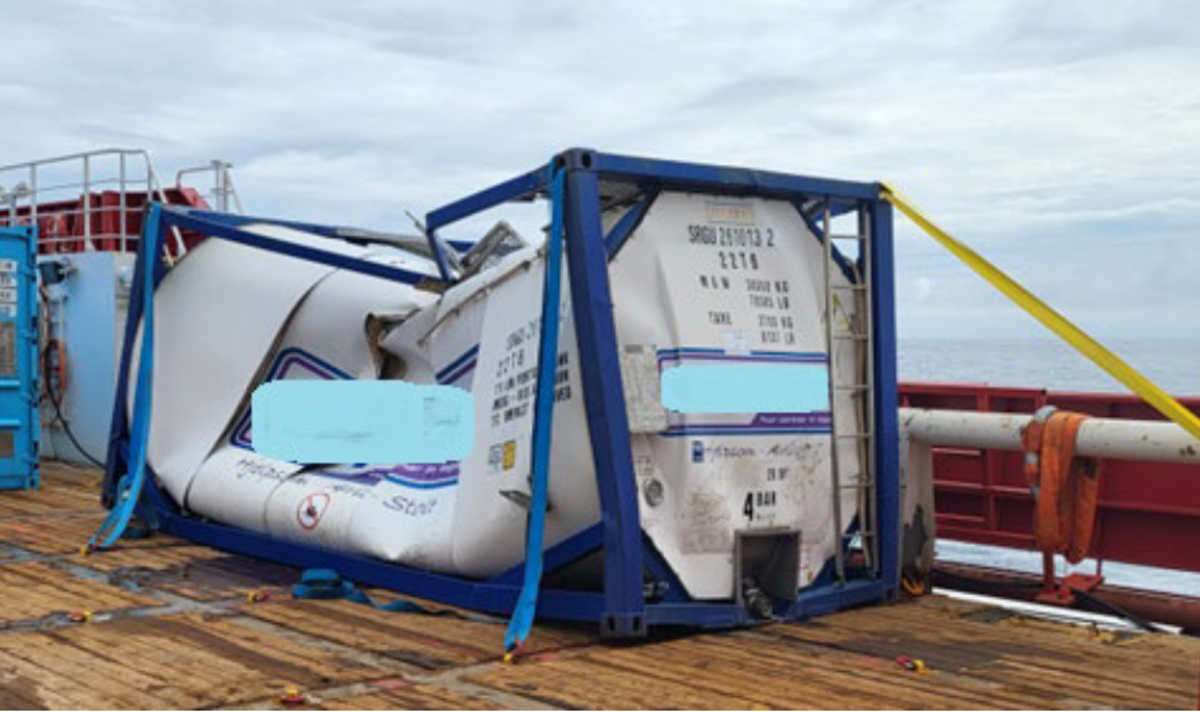
What went wrong?
The implosion happened due to a vacuum created in the tank because the MEG was pumped out into a storage reservoir on the vessel during a mobilisation.
- A 20 cubic metre tank had been planned for and agreed, but a different and larger type of tank, of 26 cubic metre capacity, was actually delivered.
- The new tank was unfamiliar to the third-party operators and no documentation was available before starting pumping operations. This type of tank requires a manual air inlet valve to be opened on top of the tank, to allow for air inlet and avoid vacuum. Due to lack of knowledge and documentation, this valve was not opened as it should have been, hence creating sufficient vacuum in the tank to cause it to implode five days later.
- The supplier of the tank and of pre-commissioning services was new to the company;
- Although the supplier had been audited before the work, the audit did not generate sufficient insight into the capabilities and experience of the supplier.
- The possible risks arising from fact that the supplier was new were not recognised in the risk assessment;
- Only a “standard” onboarding/scope familiarisation was done, there was no adaptation specific to new suppliers.
- The tank type and specification (it was a carbon fibre tank) were unknown to both the third-party operators and the suppliers.
- The suppliers’ personnel did not inform any company personnel that they were not familiar with this type of tank.
- The tank was operated without manuals/datasheet reviewed at the time.
MEG
Monoethylene glycol (MEG) is an anti-freeze widely used at wellheads and in pipelines to prevent hydrate formation at pipeline conditions, particularly where there are lower temperatures in subsea pipelines.
Actions taken
- Increased focus and follow-up of new suppliers, with specific onboarding arrangements to offshore routines and in-depth familiarisation to scope of work.
- Ensure that operators of equipment are familiarised with equipment specifications and modes of use, including risk assessment and documentation requirements.
- Ensure that Management of Change (MoC) is properly applied when equipment is changed out, also when it involves third-party equipment.
IMCA Safety Flashes summarise key safety matters and incidents, allowing lessons to be more easily learnt for the benefit of the entire offshore industry.
The effectiveness of the IMCA Safety Flash system depends on the industry sharing information and so avoiding repeat incidents. Incidents are classified according to IOGP's Life Saving Rules.
All information is anonymised or sanitised, as appropriate, and warnings for graphic content included where possible.
IMCA makes every effort to ensure both the accuracy and reliability of the information shared, but is not be liable for any guidance and/or recommendation and/or statement herein contained.
The information contained in this document does not fulfil or replace any individual's or Member's legal, regulatory or other duties or obligations in respect of their operations. Individuals and Members remain solely responsible for the safe, lawful and proper conduct of their operations.
Share your safety incidents with IMCA online. Sign-up to receive Safety Flashes straight to your email.