Lift bag near miss
- Safety Flash
- Published on 13 March 2023
- Generated on 12 July 2025
- IMCA SF 07/23
- 3 minute read
Jump to:
During the over-boarding of a spool, a lift bag while being inflated, ascended through the engineered rigging arrangement and was caught by the contingency rigging.
What happened?
The diver had rigged the lift bag inappropriately for the conditions.
The lift bag was hooked into one eye of the sling, the sling then slipped out as the lift bag became inflated and was inverted with the safety strap.
Our member considered this incident to have had the potential for a serious injury or fatality.

Spools were being rerigged subsea to gain the third wrap needed for the lift bag attachment
What went wrong?
- Assumptions were made by the diver and by the supervisor, about the rigging, perhaps owing to:
- poor visibility
- diver inexperience with lift bag operations
- complacency.
- poor visibility
- The rigging arrangements were not correct nor verified as per procedure:
- Spool rigging and local in-field adjustment began to happen without proper documentation or formal management of change (MoC).
- The divers were multi-tasking, working in different locations on different concurrent tasks, and communications between the divers and diver supervisor were complex and unclear.
- The rigging had been changed earlier but this change had not been communicated to the dive team.
- As the final spool was lowered, late at night, rigging changes were not noticed.
- Spool rigging and local in-field adjustment began to happen without proper documentation or formal management of change (MoC).
- Existing procedures were not specific to this task:
- A 4-ton lift bag was identified in the procedure but was not available.
- The inverter rigging was not one size fit all, as the bags were different sizes, thus creating a scenario where diver rigging was required to lengthen or shorten the existing rigging.
- A 4-ton lift bag was identified in the procedure but was not available.
- There were changes of personnel during the job:
- Superintendents were changed out.
- The bell run was split such that the diver that de-rigged the spool was not the same diver as inflated the lift bag that came loose.
- Superintendents were changed out.
- During the job, a finger incident occurred on the bell clump basket, and there was a safety stand down.
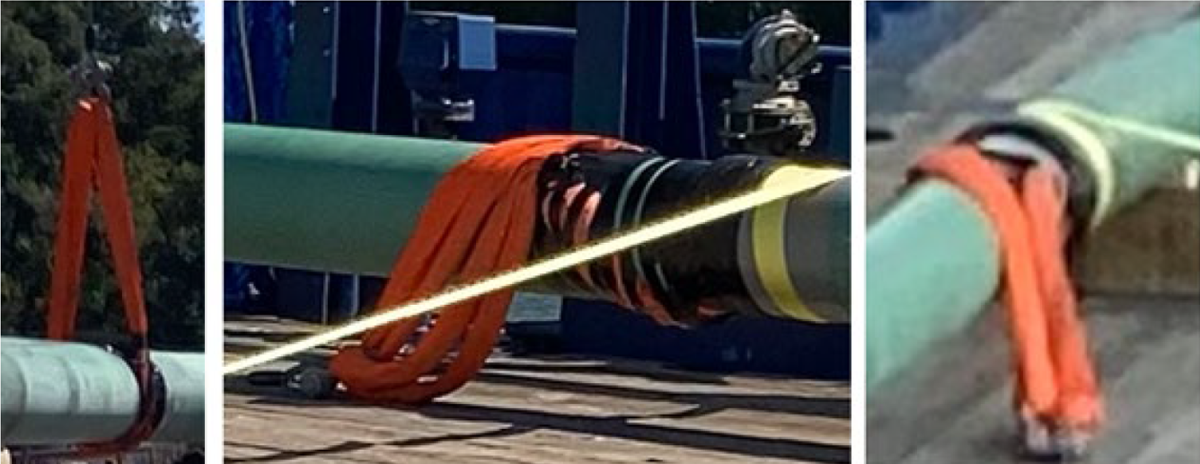
Black duct tape added to “hold” the rigging in place
Lessons learned
- Ensure one single person is accountable for rigging, reporting to the Superintendent and collaborating with the dive team.
- Improve management and installation of rigging configurations.
- Ensure written procedures are not generic, are up to date, and reflect the details of the task in hand.
- Minimise multitasking to eliminate distractions and fatigue.
- Be additionally vigilant and ensure there is thorough communication:
- at crew change and at shift change
- between shore-side or yard and vessel
- between crew of different departments – dive, deck, bridge, project, etc.
- at crew change and at shift change
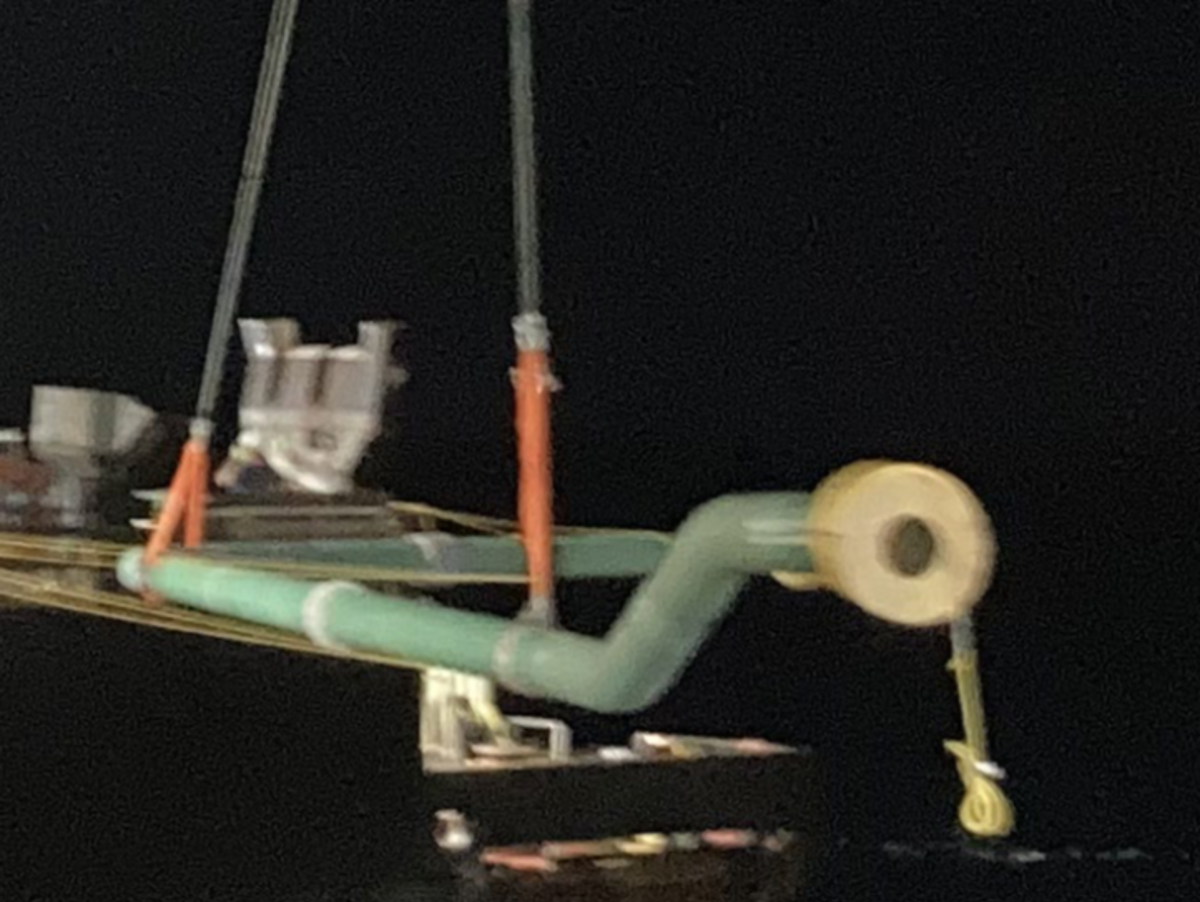
Note the middle leg is not choked, as per the drawing, change not noticed, nor articulated to the divers
Related Safety Flashes
-
IMCA SF 05/12
8 June 2012
-
IMCA SF 03/10
28 May 2010
-
IMCA SF 12/09
17 August 2009
IMCA Safety Flashes summarise key safety matters and incidents, allowing lessons to be more easily learnt for the benefit of the entire offshore industry.
The effectiveness of the IMCA Safety Flash system depends on the industry sharing information and so avoiding repeat incidents. Incidents are classified according to IOGP's Life Saving Rules.
All information is anonymised or sanitised, as appropriate, and warnings for graphic content included where possible.
IMCA makes every effort to ensure both the accuracy and reliability of the information shared, but is not be liable for any guidance and/or recommendation and/or statement herein contained.
The information contained in this document does not fulfil or replace any individual's or Member's legal, regulatory or other duties or obligations in respect of their operations. Individuals and Members remain solely responsible for the safe, lawful and proper conduct of their operations.
Share your safety incidents with IMCA online. Sign-up to receive Safety Flashes straight to your email.