Diver’s worksite identification errors
- Safety Flash
- Published on 3 May 2017
- Generated on 12 July 2025
- IMCA SF 09/17
- 3 minute read
Jump to:
A member reports continued worksite identification errors by divers.
What's happening?
The errors occur in spite of a significant reduction in such errors following improved engineering procedures and the application of operational good practice.
Mistakes are still being made, primarily when returning to the worksite after an initial correct identification.
Example 1:
During a recent dive, a Tronic connector was correctly identified by the diver on the panel with its corresponding jumper tail labelled back from the connector.
Positive confirmation was provided by the team in Dive Control.
There followed an unsuccessful attempt to loosen and remove this connector with a C-spanner.
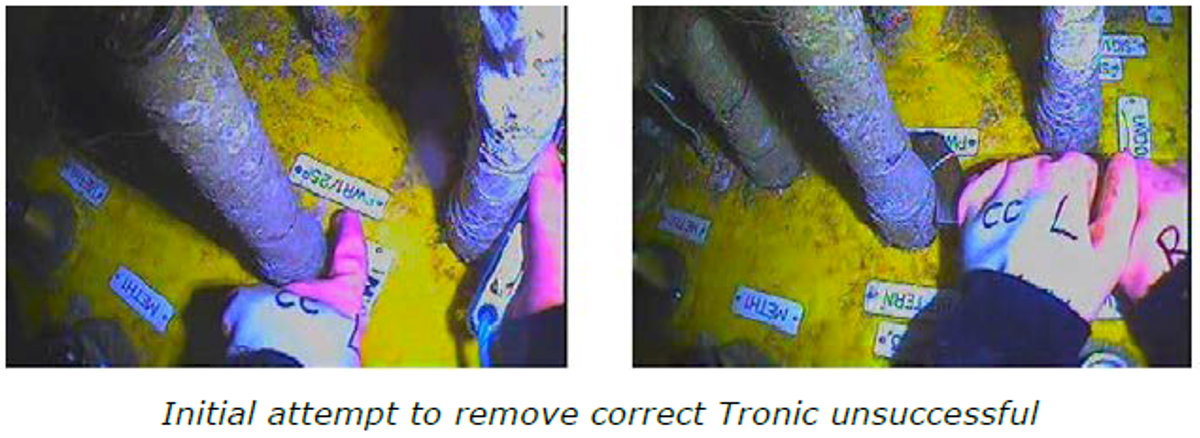
In order to provide more leverage, it was decided to try a strap wrench so the diver moved away from the worksite to collect this tool.
Crucially, the C-spanner was left on a different but adjacent connector and when the diver returned with the strap wrench he mistook this connector for the one previously identified.
The error went un-noticed and the diver removed and cleaned the wrong connector.

The mistake was noticed while preparing to connect the jumper to the wrong port as the colours did not match. The job was immediately stopped and a “Time Out For Safety” held, before retracing the steps and continuing with the correct Tronic connector.
At no time was the diver or equipment at risk as the power was isolated.
Example 2:
Planned operations for removal of a section of pipework from a flange took two dives.
The section to be removed was correctly identified during Dive number 1, but after bell turnaround and the meal break, during Dive 2, the incorrect flange was identified and the wrong bolts were removed.
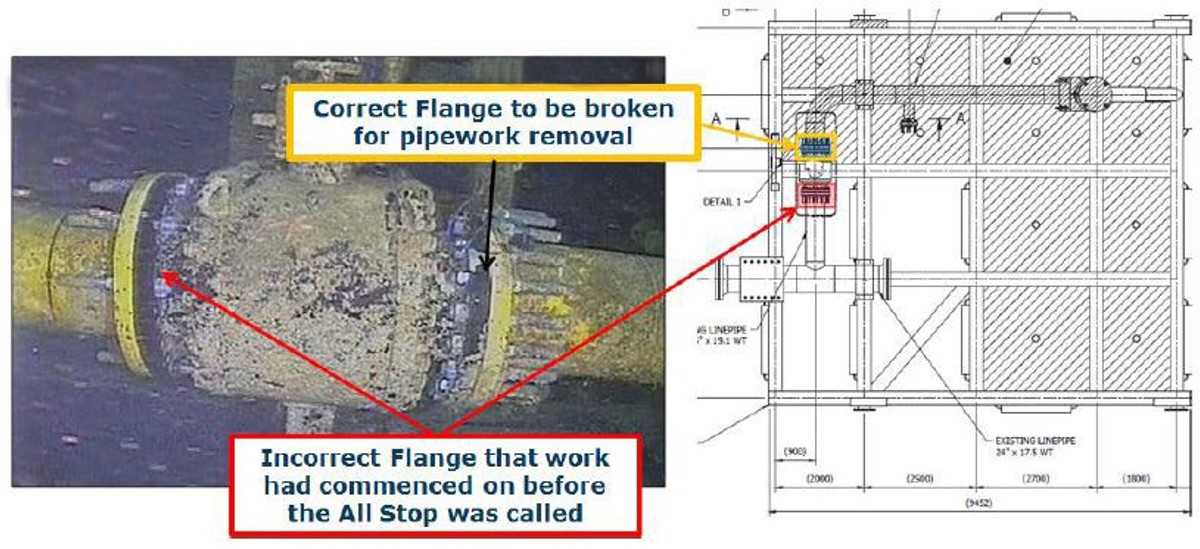
After several bolts had been removed, the Dive Supervisor called an “All Stop”, as it was identified that work was being conducted on the wrong flange. A “Time Out for Safety” was called to discuss actions already taken and to agree the further actions needed. At no time were the divers or equipment at risk as the Pipeline End Manifold was shut down.
Our member notes that both of these recent incidents have their own set of contributory factors such as inadequate handover between Dive Supervisors in the second example, but both events featured identical failings which were consistent with previous incidents.
Actions
- Increase focus/attention in setting up for worksite identification.
- Procedures and task plans should include steps to positively identify and mark the specific item to be worked on.
- Dive Supervisors should ensure the specific item to be worked on is positively identified and appropriately marked for intervention.
- Should the worksite be left, even momentarily, the item to be worked on should be reacquired and again positively identified before work resumes.
Related safety flashes
-
IMCA SF 33/16
6 December 2016
-
IMCA SF 23/16
13 September 2016
IMCA Safety Flashes summarise key safety matters and incidents, allowing lessons to be more easily learnt for the benefit of the entire offshore industry.
The effectiveness of the IMCA Safety Flash system depends on the industry sharing information and so avoiding repeat incidents. Incidents are classified according to IOGP's Life Saving Rules.
All information is anonymised or sanitised, as appropriate, and warnings for graphic content included where possible.
IMCA makes every effort to ensure both the accuracy and reliability of the information shared, but is not be liable for any guidance and/or recommendation and/or statement herein contained.
The information contained in this document does not fulfil or replace any individual's or Member's legal, regulatory or other duties or obligations in respect of their operations. Individuals and Members remain solely responsible for the safe, lawful and proper conduct of their operations.
Share your safety incidents with IMCA online. Sign-up to receive Safety Flashes straight to your email.