Incorrectly selected oxygen welding gas hose bursts & catches fire
- Safety Flash
- Published on 9 May 2018
- Generated on 12 July 2025
- IMCA SF 10/18
- 2 minute read
Jump to:
The ship’s welder opened the Oxygen and Acetylene gas bottle valves in order to do a cutting job on deck.
What happened?
These gas bottles were attached to the vessel’s integrated welding gas system. Opening the valve on the Oxygen bottle had the immediate effect of causing an explosion to a short, high pressure hose delivering oxygen from the bottle to the oxygen gas regulator. The end of the hose caught fire and was quickly extinguished by turning off the oxygen bottle. Nobody was injured and the only damage was to the hose that completely separated.
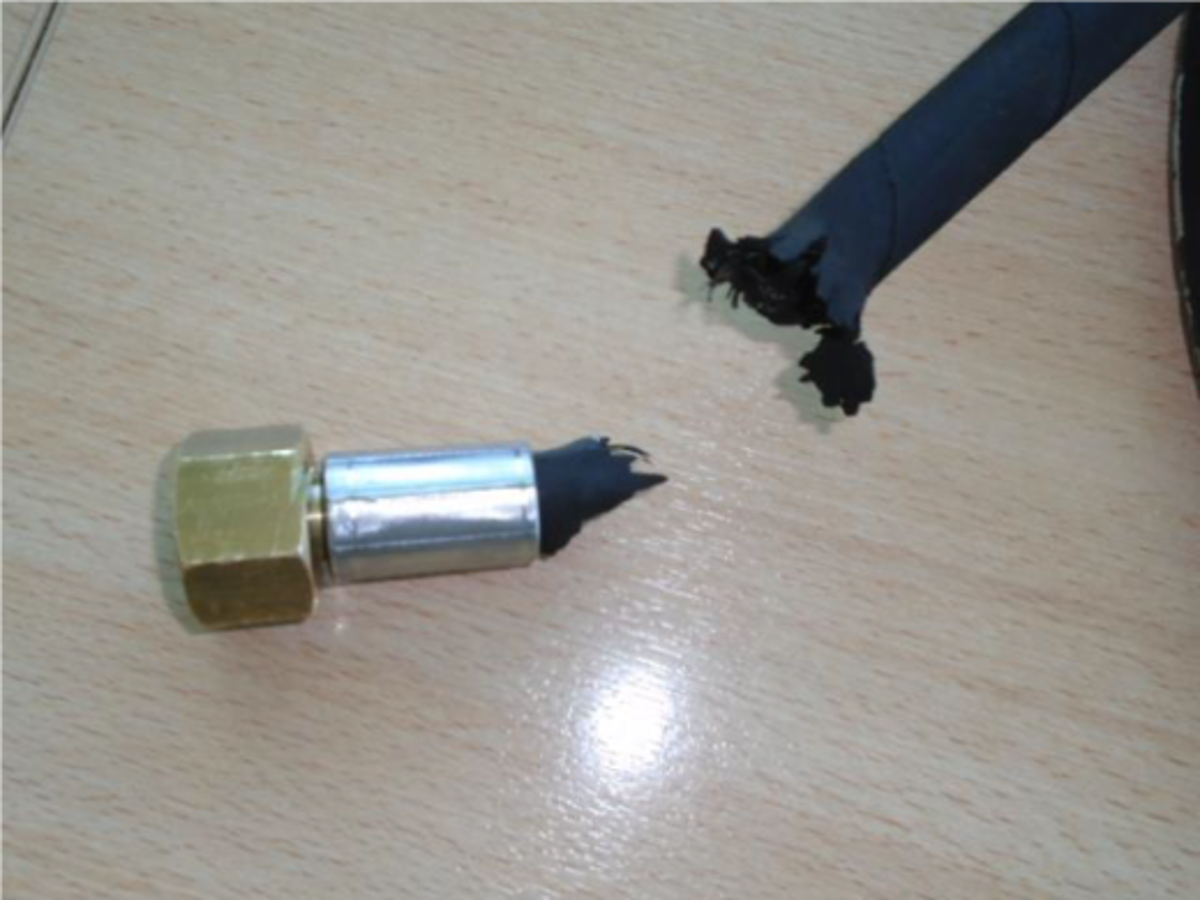
What went wrong?
Investigation found the following:
- The hose had been recently replaced, but the replacement hose was a hydraulic oil service hose with oxygen fittings. The replacement hose was not compliant with the ISO 14113 specification required by the manufacturer, although the pressure rating was suitable.
- The non-compliant hose was supplied from a non-preferred supplier (the required hose length was not available from original supplier).
- The onboard team did not adequately check that the hose was of the correct specification.
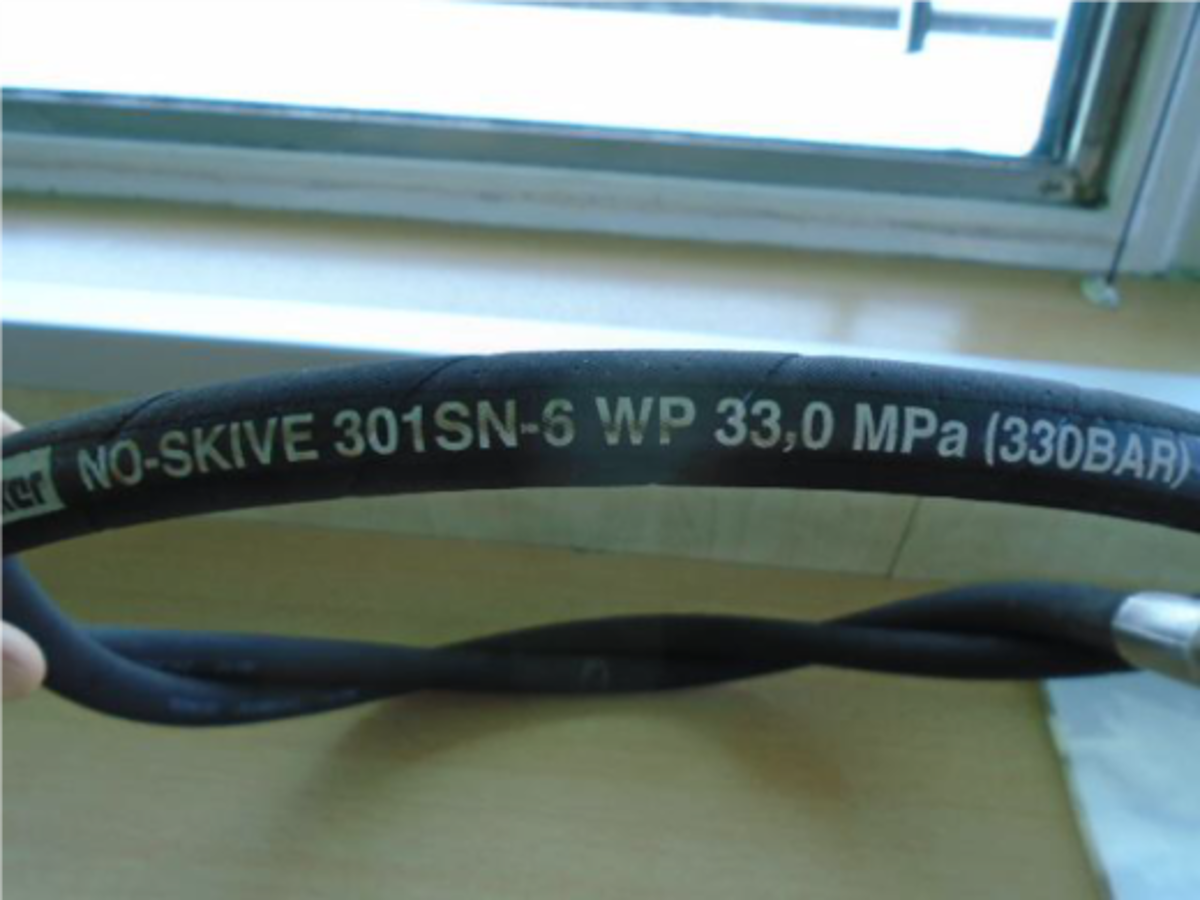
What was the cause?
Based on detailed investigation into a similar incident, it was suggested that the cause of the incident was due to adiabatic compression heating within the hose which caused the inner lining to auto-ignite due to residual oil within the hose. Our member notes that there are numerous incidents recorded by industry due to this issue.
What actions were taken? What lessons were learned?
Welding hoses should be compliant with ISO 14113. For oxygen hoses, the material should have an auto-ignition temperature suitable for the service (typically > 400 °), and cleaned for oxygen service.
- Do not assume that because a hose is sufficiently pressure rated it is fit for a specific purpose.
- Always ensure correct specification hoses are ordered and received.
IMCA notes that in order to avoid adiabatic compression:
- Use only original equipment and spares when handling/servicing oxygen equipment.
- Work clean – no oil or any other hydrocarbon impurities must contaminate the parts (your hands, tools etc).
- Open oxygen cylinder top valves slowly.
Related Safety Flashes
-
IMCA SF 20/17
11 August 2017
-
-
IMCA SF 21/16
10 August 2016
IMCA Safety Flashes summarise key safety matters and incidents, allowing lessons to be more easily learnt for the benefit of the entire offshore industry.
The effectiveness of the IMCA Safety Flash system depends on the industry sharing information and so avoiding repeat incidents. Incidents are classified according to IOGP's Life Saving Rules.
All information is anonymised or sanitised, as appropriate, and warnings for graphic content included where possible.
IMCA makes every effort to ensure both the accuracy and reliability of the information shared, but is not be liable for any guidance and/or recommendation and/or statement herein contained.
The information contained in this document does not fulfil or replace any individual's or Member's legal, regulatory or other duties or obligations in respect of their operations. Individuals and Members remain solely responsible for the safe, lawful and proper conduct of their operations.
Share your safety incidents with IMCA online. Sign-up to receive Safety Flashes straight to your email.