Dropped object: Dislodged flex-joint laydown tool component
- Safety Flash
- Published on 25 November 2021
- Generated on 4 July 2025
- IMCA SF 32/21
- 2 minute read
Jump to:
During removal of the anti-rotation / laydown tool from a Flex-Joint, a load-ring half plate, weighing 85 kg, was inadvertently dislodged and dropped about 1.8 m to deck.
What happened?
Crew on a J-Lay Tower were removing the anti-rotation device / laydown. The tower was tilted to 5 degrees at the time of the incident. A team of riggers and technicians proceeded to remove the half plates, which form part of the laydown tool.
After the load ring securing plate was removed and the final jacking bolt had been loosened, one load ring element slid out of the assembly and dropped down onto deck.
There were two persons close to the dropped half ring. No one was injured during the incident.
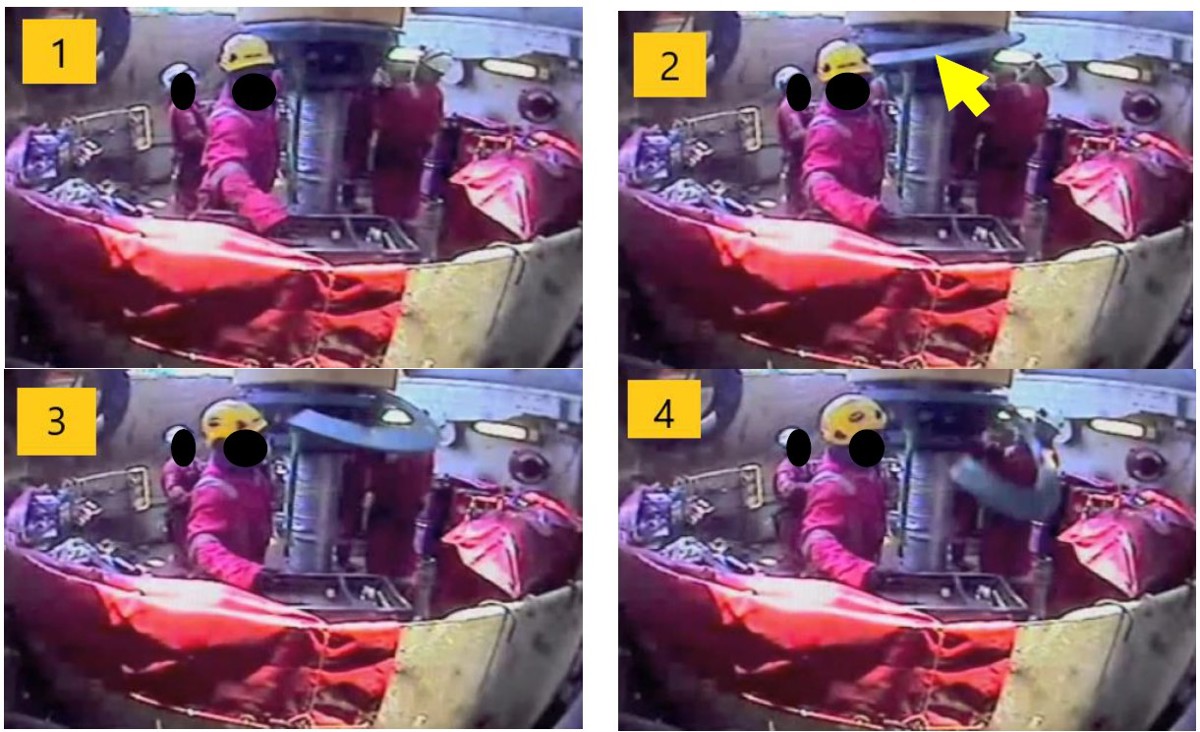
Photographs: CCTV footage capturing the moment the load ring half plate, indicated by the yellow arrow, was dislodged from the laydown tool assembly image 1 and the subsequent trajectory of the dropped object (images 2,3 and 4)
What went wrong?
Procedures not followed:
- The removal of the load ring plates did not follow the approved procedure. The task plan included the manufacturer’s procedure which described the correct way to do it, which required eye bolts and rigging to remove the section of the laydown tool using a crane.
- The task of removing the load ring half plates manually/by hand was deemed to be faster and required less steps than the approved procedure.
- The risk associated with the removal of the heavy load rings by hand instead of using a crane was not assessed.
Actions
- Follow the instructions; keep to the procedures!!
- Any planned changes to the task plan or procedure should require a Management of Change process to be conducted to assess the risks from the change, apply the appropriate controls and gain authorisation to proceed.
- If unsure of the correct method to execute a task, or the associated risks, personnel should always speak to their supervisor before attempting the task – don’t be afraid to STOP THE JOB.
Related Safety Flashes
-
IMCA SF 28/21
15 October 2021
-
-
IMCA SF 05/20
13 February 2020
-
-
IMCA SF 22/19
17 September 2019
-
IMCA Safety Flashes summarise key safety matters and incidents, allowing lessons to be more easily learnt for the benefit of the entire offshore industry.
The effectiveness of the IMCA Safety Flash system depends on the industry sharing information and so avoiding repeat incidents. Incidents are classified according to IOGP's Life Saving Rules.
All information is anonymised or sanitised, as appropriate, and warnings for graphic content included where possible.
IMCA makes every effort to ensure both the accuracy and reliability of the information shared, but is not be liable for any guidance and/or recommendation and/or statement herein contained.
The information contained in this document does not fulfil or replace any individual's or Member's legal, regulatory or other duties or obligations in respect of their operations. Individuals and Members remain solely responsible for the safe, lawful and proper conduct of their operations.
Share your safety incidents with IMCA online. Sign-up to receive Safety Flashes straight to your email.