Fatality results from incorrect handling of equipment
- Safety Flash
- Published on 1 February 2003
- Generated on 2 July 2025
- IMCA SF 02/03
- 3 minute read
Jump to:
IMCA has been advised of a fatality that occurred at a shipyard during the construction of an FSO, while an electrical panel was being moved with the aid of rollers.
What happened?
The electrical panel weighed 1.8 tonnes, was 2.5 metres high and had a base measuring 2.75m x 0.2m. The bottom was an open arrangement with a flat bar at its edge.
The method of movement was to put the panel on four independent rollers – one under each corner of the panel bottom.
After lifting the panel onto a temporary platform and setting it on the four rollers, five workers started to push the panel into the switchboard room. The panel was still connected to the crane with workers positioned around the panel. After moving the panel about one third of the way into the room, it was impossible to keep the crane connected due to roof overhang. After removing the rigging, the work crew continued the transfer process.
After 3m transfer into the room, the panel bottom lost contact with one of the rollers, becoming destabilised. The panel toppled over and trapped one of the workers. He was crushed and died instantly.
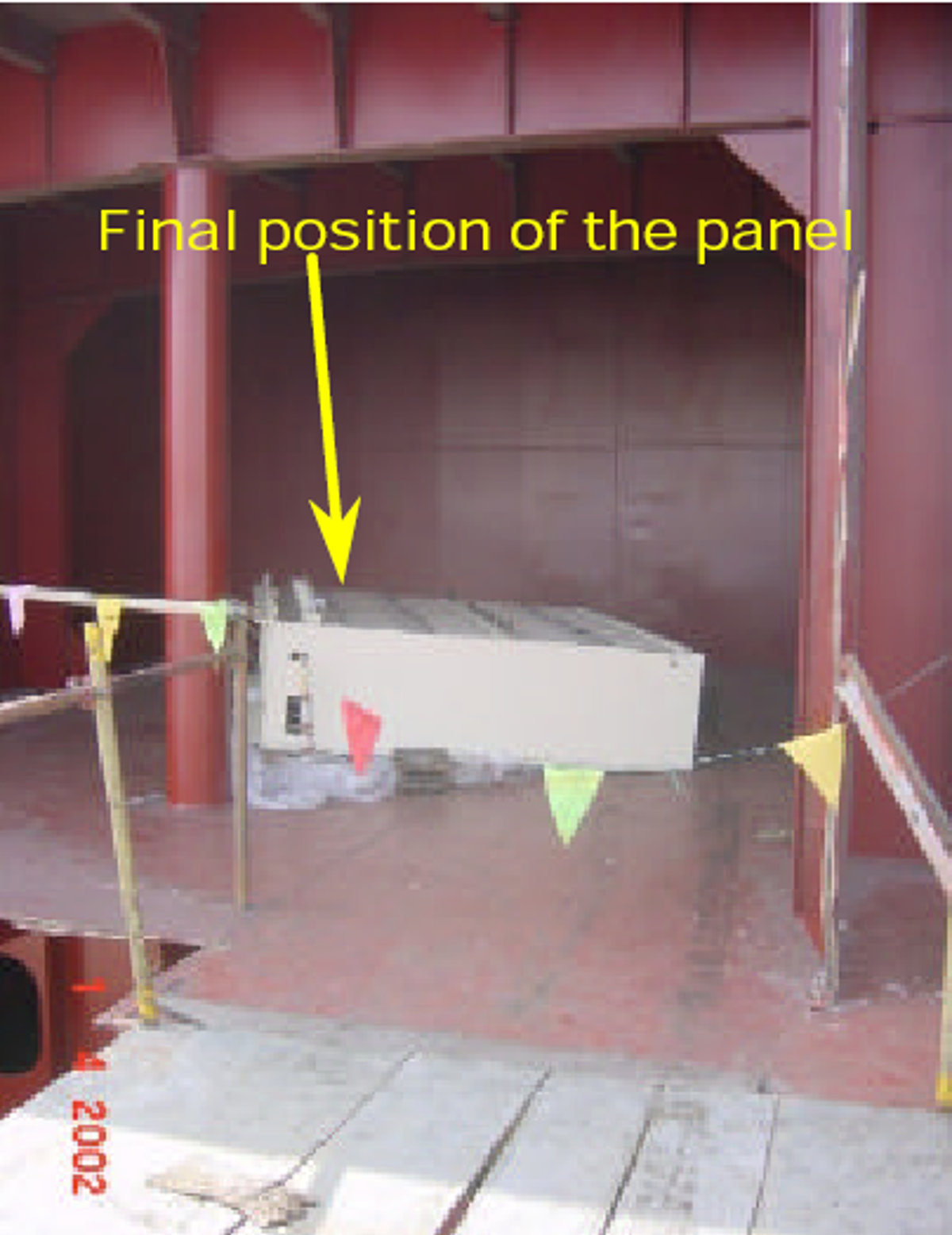
The resulting investigation identified the following causes and contributory factors:
- The contact point on the roller was very small, with a high centre of gravity and a small footprint area.
- The rollers were independent and not guided, needing to be kept in position under the panel by the workers.
- The rollers had not been adequately maintained and some were not rolling properly.
- The workers were not experienced in use of the rollers.
- There was an apparently lack of safety awareness at each level of the shipyard’s management.
The company involved has noted the following follow-up actions needed:
- Adequate safety training of workers to be conducted and the importance of safety to be stressed to management.
- Preventive measures to be taken and adequate preparations made before the commencement of work.
- A procedure on the use of rollers to be inserted into the company’s operations manual.
- Tools and equipment to be checked before use and a preventive maintenance policy implemented to make sure that equipment and tools are in a good condition.
- Daily ‘toolbox talks’ to be instigated involving workers and supervisors, typically covering the following:
- objectives of the work (including whether it is covered by a permit to work).
- details of the individual activities covered the individual activities comprising the overall task.
- who is involved in the task and what are each person’s responsibilities.
- what equipment will be used and its condition.
- what other task(s) will be performed simultaneously in the area by others.
- what hazards are associated with the work and what control measures can be taken to minimise any risks, including what personal protective equipment (PPE) required and its condition.
- whether any dangerous substances (e.g. chemicals) are involved and particular precautions needed for them.
- whether or not weather conditions will affect the work.
- finally, does everyone understand the task, the safety aspects covered above and are there any concerns not already addressed?
IMCA Safety Flashes summarise key safety matters and incidents, allowing lessons to be more easily learnt for the benefit of the entire offshore industry.
The effectiveness of the IMCA Safety Flash system depends on the industry sharing information and so avoiding repeat incidents. Incidents are classified according to IOGP's Life Saving Rules.
All information is anonymised or sanitised, as appropriate, and warnings for graphic content included where possible.
IMCA makes every effort to ensure both the accuracy and reliability of the information shared, but is not be liable for any guidance and/or recommendation and/or statement herein contained.
The information contained in this document does not fulfil or replace any individual's or Member's legal, regulatory or other duties or obligations in respect of their operations. Individuals and Members remain solely responsible for the safe, lawful and proper conduct of their operations.
Share your safety incidents with IMCA online. Sign-up to receive Safety Flashes straight to your email.