Loss of heading control on an FPU during diving operations
- Safety Flash
- Published on 27 March 2024
- Generated on 3 July 2025
- IMCA SF 07/24
- 3 minute read
Jump to:
The only thruster in operation and available was the aft port thruster.
What happened?
During diving operations at an FPU (floating production unit), the forward thruster was isolated, and the turret locked, in line with diving isolation procedures. The starboard aft thruster was out of service due to an ongoing upgrade project. The only thruster in operation and available was the aft port thruster.
During preparation of greasing of the port thruster steering pump, the standby pump did not start automatically. This resulted in there being no azimuth (direction) control of the thruster and loss of heading control of the FPU. The Diving Supervisor on the light daughter craft (LDC) was notified by the FPU control room immediately that they had lost power on one thruster. The Diving Supervisor informed the divers of the situation and confirmed that the divers had a clear route to surface.
Photo
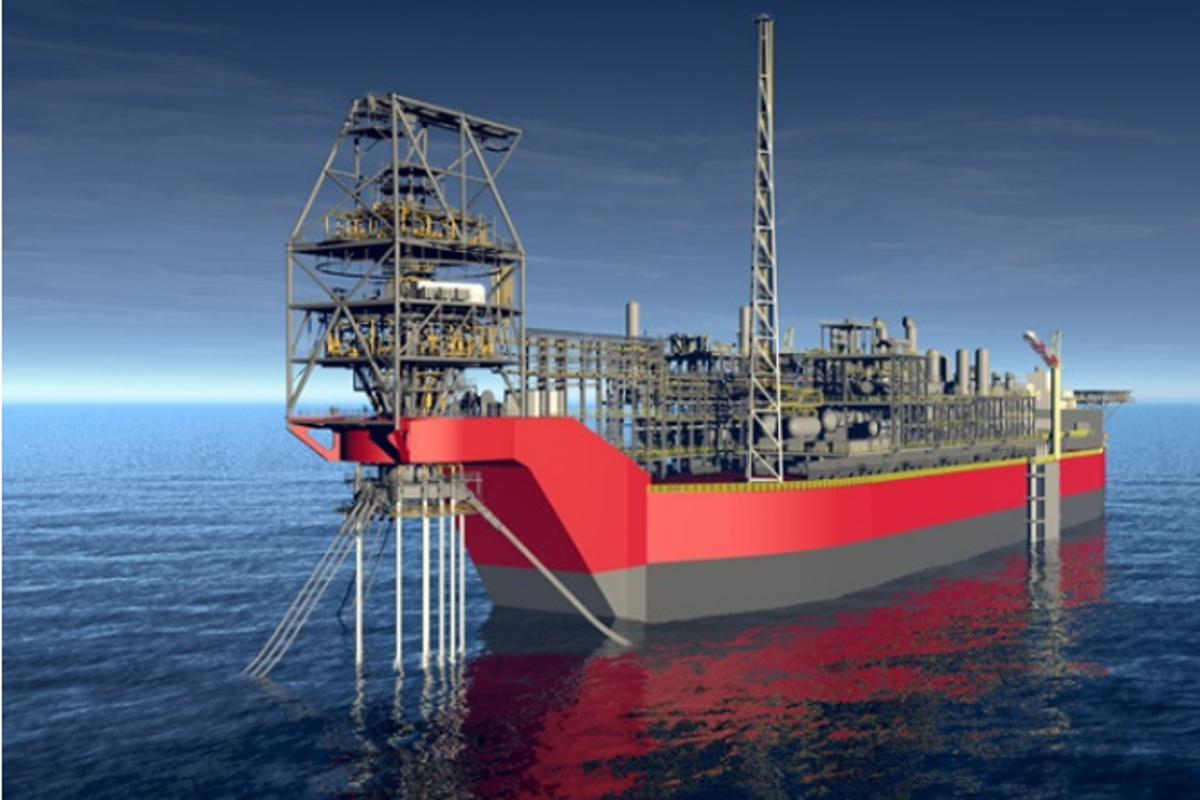
Typical FPU Image: https://oilandgas.world/
Based on the fact that the FPU turret rotation was locked, the Diving Supervisor secured the work site, while the LDC Coxswain monitored the heading. The Diving Supervisor then recovered the divers to surface safely in a controlled manner.
What went right?
The dive was aborted and divers safely recovered to surface.
What went wrong?
Our member noted that usually maintenance would not be performed on the thruster equipment while only one was in service and during diving operations. Greasing of the main steering pump was not usually a permitted activity, as the crew would normally switch from main to standby and then grease the offline unit so that there was no interruption in the steering. Also there was no requirement for Lock-out/Tag-out (LOTO) of the standby unit. However, in this case the standby pump did not produce pressure and the other pump, which had become the standby, did not auto-start.
Our member notes that there was:
- Insufficient risk assessment: of both heading control and of the Emergency Preparedness Plan.
- It was unclear to the FPU control room team whether or not there were divers were in the water.
- Tasks seen as routine: Greasing was not an activity that was usually discussed in the work permit/SIMOPS meeting as it was seen as operational and did not require a Permit to work.
- Our member notes that the notification from the FPU control room of the severity of the incident, was unclear.
What were the causes?
- Diving operations were on-going at the FPU whilst there was only one only thruster in operation and available.
- The FPU was lying with the wind to its side to shelter the LDC.
- During planned greasing, equipment (the standby pump) did not automatically start as it should have done, leading to there being no azimuth control (direction) of the thruster and hence loss of heading control of the FPU.
Lessons learned
- Renewed focus on understanding of possible consequences of working on any critical equipment (thrusters, generators etc) during diving or marine operations.
- Amend company SIMOPS matrix with regard to the possible impact maintenance on critical equipment for position keeping (thrusters, generators, critical utilities etc) could have during vessel and diving operations.
Related Safety Flashes
-
IMCA SF 28/23
6 December 2023
-
IMCA Safety Flashes summarise key safety matters and incidents, allowing lessons to be more easily learnt for the benefit of the entire offshore industry.
The effectiveness of the IMCA Safety Flash system depends on the industry sharing information and so avoiding repeat incidents. Incidents are classified according to IOGP's Life Saving Rules.
All information is anonymised or sanitised, as appropriate, and warnings for graphic content included where possible.
IMCA makes every effort to ensure both the accuracy and reliability of the information shared, but is not be liable for any guidance and/or recommendation and/or statement herein contained.
The information contained in this document does not fulfil or replace any individual's or Member's legal, regulatory or other duties or obligations in respect of their operations. Individuals and Members remain solely responsible for the safe, lawful and proper conduct of their operations.
Share your safety incidents with IMCA online. Sign-up to receive Safety Flashes straight to your email.