Partial parting of a bell main lift wire
- Safety Flash
- Published on 24 April 2008
- Generated on 30 June 2025
- IMCA SF 08/08
- 3 minute read
Jump to:
A Member has reported the partial parting of a bell main lift wire.
What happened?
During bell recovery a member of the dive team noticed damage on the bell main lift wire, 48m from the bell.
The bell recovery was stopped, the bell guide weights were brought up to support the bell, strands of damaged wire were removed by the diving technicians and deck crew and the bell was lifted using the bell guide wire. The bell was then locked into the cursor and safely clamped on to the system.
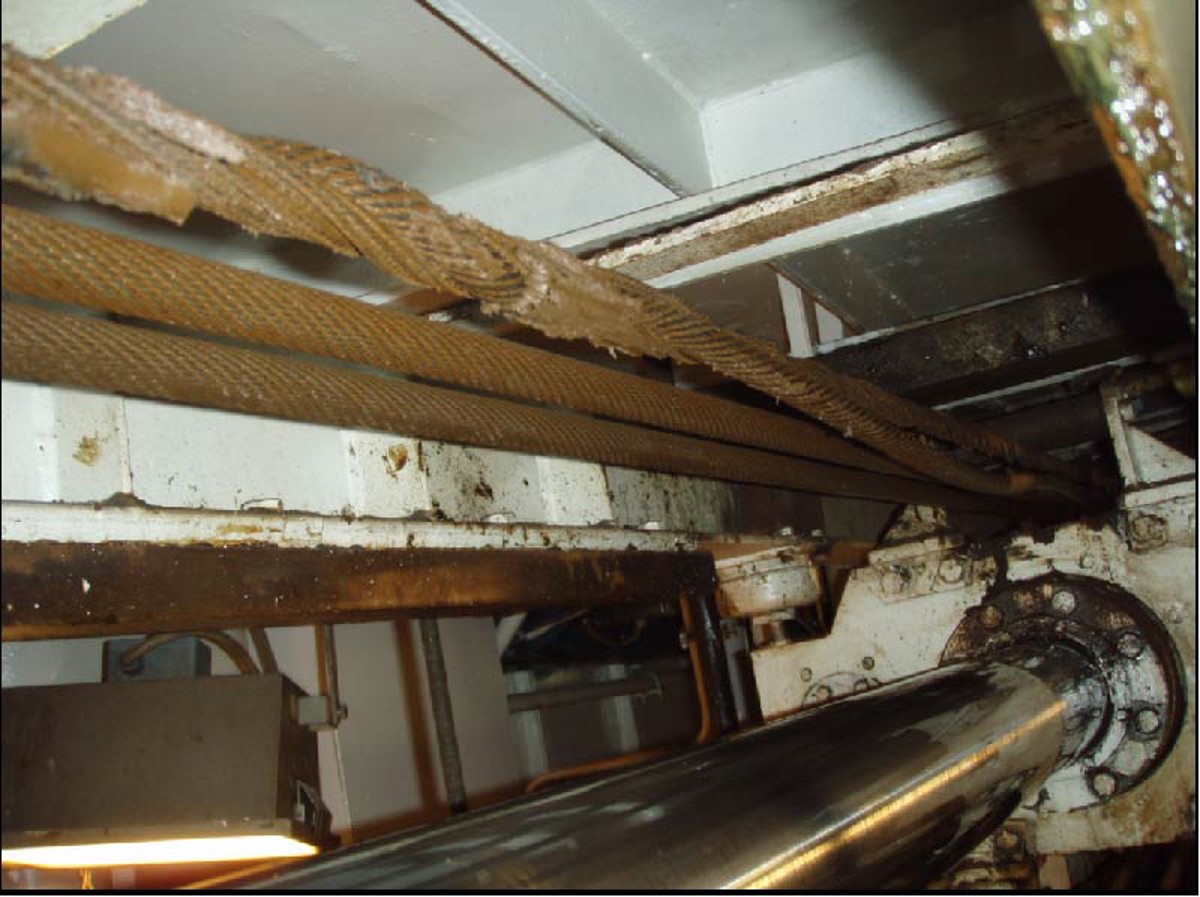
Photograph showing partly parted wire
After investigation by the company involved, the following points were highlighted:
- The cause of the wire rope failure was internal corrosion damage where the inner core wires of the rope had been reduced in size by up to 50% with no external damage visible.
- The rope lubricant had been lost internally and the galvanised coating was no longer present. Both of these two factors had accelerated the corrosion of the wires.
- The local corrosion of the core wires had led to a loss in diameter and strength. The loss in strength had resulted in overload of the individual wires and placed additional stress on the core.
When checking the size of the bell wire (nominally 22mm diameter) approximately 3m each side of the damaged area, the diameter was recorded as 21mm. At various other areas of the wire the readings were between 21.3mm and 21.8mm.
ISO 4309 2004 paragraph 3.5.7 allows for a 3% reduction for multi strand wire making 21mm outside acceptable tolerances.
Even though the wire inspection, testing and maintenance procedures used by the company were in accordance with local legislation, IMCA guidance and company procedures, the deterioration of the wire failed to be detected.
The company noted that inspections had been carried out for the wire at six monthly intervals, annual destructive tests had been carried out, a comment regarding lack of lubrication had been noted in last report of destructive testing and pressure lubrication of the wire had been carried out at six-month intervals.
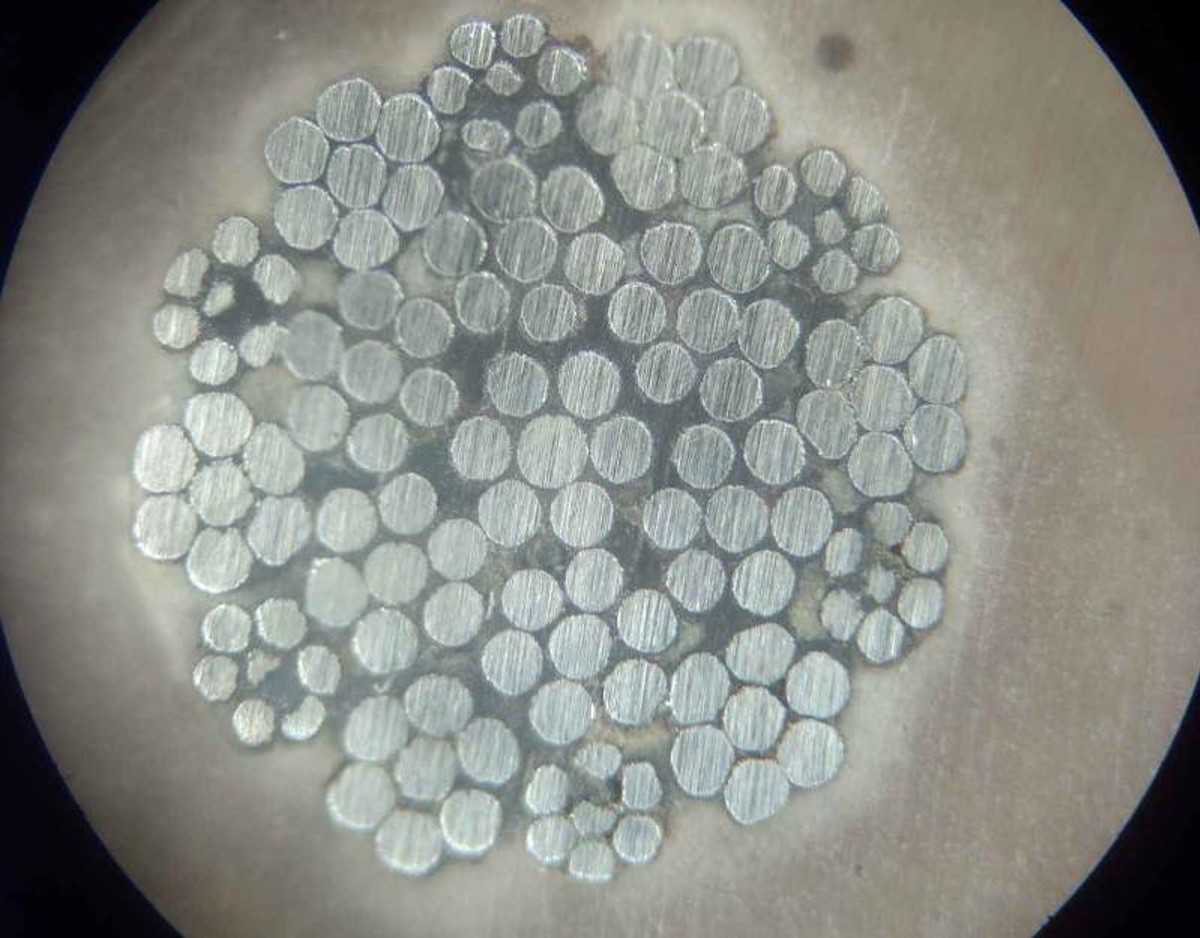
Photograph of a section taken from the core of the rope close to the fracture
Possible contributory factors to the failure of the bell wire identified by the member company were:
- The extent of the detrimental effect of multiple sheaves and sheave diameters in use.
- The wire rope had, over a number of years, been bent over heave compensator sheaves which could have led to internal fretting taking place within the rope once the rope lubricant had been lost.
- High peak loads could have been experienced on the system when the heave compensators were fully compressed before the bell and cursor were handled in moon-pool.
- The bell wire was eight years old which was inside the company’s discard policy of ten years which may need to be re-assessed.
Members are urged to consider all of the points raised and review their own wire rope maintenance and testing policies as appropriate.
IMCA Safety Flashes summarise key safety matters and incidents, allowing lessons to be more easily learnt for the benefit of the entire offshore industry.
The effectiveness of the IMCA Safety Flash system depends on the industry sharing information and so avoiding repeat incidents. Incidents are classified according to IOGP's Life Saving Rules.
All information is anonymised or sanitised, as appropriate, and warnings for graphic content included where possible.
IMCA makes every effort to ensure both the accuracy and reliability of the information shared, but is not be liable for any guidance and/or recommendation and/or statement herein contained.
The information contained in this document does not fulfil or replace any individual's or Member's legal, regulatory or other duties or obligations in respect of their operations. Individuals and Members remain solely responsible for the safe, lawful and proper conduct of their operations.
Share your safety incidents with IMCA online. Sign-up to receive Safety Flashes straight to your email.