Lost time injury (LTI): Thumb injury
- Safety Flash
- Published on 25 November 2011
- Generated on 2 July 2025
- IMCA SF 13/11
- 4 minute read
Jump to:
A Member has reported an incident in which a member of the crew sustained a lost time injury (LTI) to his thumb.
The incident occurred when a vessel’s marine engineering team was conducting a water leak repair on part of one of the main engines during a vessel transit. The repair involved the removal of the piston and connecting rod arrangement, as well as the removal of the cylinder liner, to allow for cleaning and re-sealing. Whilst removing the piston and connecting rod, the injured person had his hands inside the engine crank case to stabilise the bottom of the connecting rod and prevent it causing damage as it passed the bottom of the cylinder liner.
The removal of the piston was accomplished using a 1Te chain block attached to the piston crown. At this stage of the operation, the injured person was on the starboard side of the engine and all the other team members were on the port side with various other duties. Communication was by means of hand signals: owing to the high noise levels in the engine room, clear verbal communication was not possible.
As another crew member started hauling up on the chain block, lifting the piston and connecting rod, the injured person found his left thumb trapped between the bottom of the cylinder liner and the bottom of the connecting rod. He motioned with his free hand to lower the load which allowed his injured thumb to be released. He then reported to the medic where, following a medical examination, he was subsequently medevaced ashore.
Although this task was not viewed as ‘routine’ maintenance, it had taken place many times before. The team consisted of four experienced members including the 2nd engineer, a rating and two fitters. The injured person was the supervisor for the shift during the maintenance task. A permit to work (PTW) and risk assessment had been completed for this task and all crew members involved had been present for the toolbox talk before it was started.
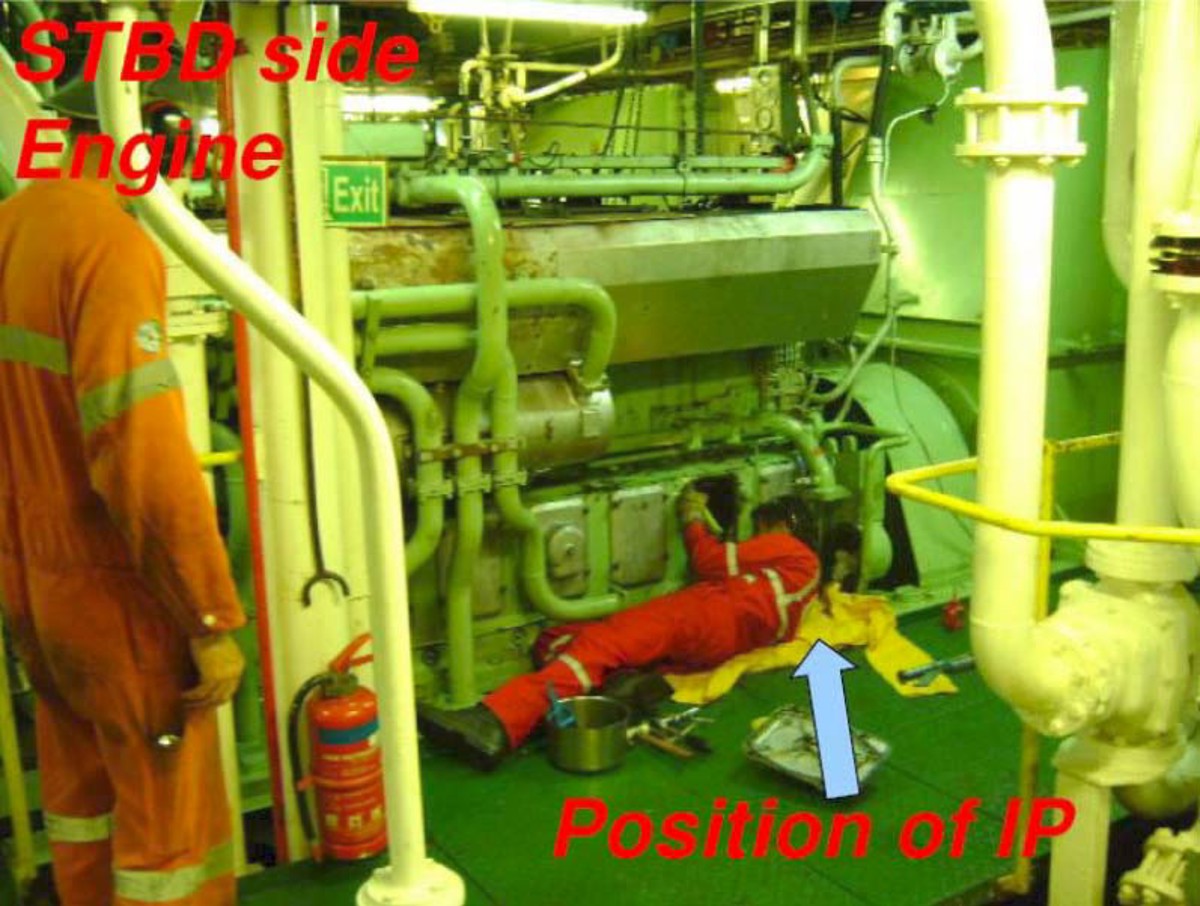
position of the injured person at the time of the incident (re-enactment)
What were the causes?
Following investigation, the company identified the following causes:
- Lack of organisation
- This meant that the injured person was the supervisor but also ended up taking a hands-on role in the operation. As the injured party was the team leader, and also taking a key part in the operation, this reduced the level of co-ordination of the task and its associated hazards.
- This meant that the injured person was the supervisor but also ended up taking a hands-on role in the operation. As the injured party was the team leader, and also taking a key part in the operation, this reduced the level of co-ordination of the task and its associated hazards.
- Lack of hazard awareness and risk perception
- Though existing controls and safety management systems were followed, they failed to identify and allow clear communication of the potential hazards involved in this operation.
- The risk assessment did not readily recognise the potential for pinch points or dropped loads during this task.
- Though existing controls and safety management systems were followed, they failed to identify and allow clear communication of the potential hazards involved in this operation.
- Poor communication in noisy engine room environment
- Control and co-ordination of the task was reduced due to the difficulty in clear communication.
- This lack of control and co-ordination during the operation allowed the load to be moved while the injured person had his hands on the connecting rod.
- The crew member controlling the load by means of the chain block had no clear line of sight to the injured person whose hands were inside the engine.
- Incorrect positioning of hands
- The injured person’s thumb was in the pinch point during movement of the load.
Actions
The following actions were taken:
- Review relevant task related risk assessments to ensure all associated and potential hazards are clearly identified and recorded.
- Ensure all lifting equipment is correctly rated and inspected for the intended task prior to use.
- Communicate the importance of toolbox talks and safe working practices to ensure key hazards are identified, discussed and addressed.
IMCA Safety Flashes summarise key safety matters and incidents, allowing lessons to be more easily learnt for the benefit of the entire offshore industry.
The effectiveness of the IMCA Safety Flash system depends on the industry sharing information and so avoiding repeat incidents. Incidents are classified according to IOGP's Life Saving Rules.
All information is anonymised or sanitised, as appropriate, and warnings for graphic content included where possible.
IMCA makes every effort to ensure both the accuracy and reliability of the information shared, but is not be liable for any guidance and/or recommendation and/or statement herein contained.
The information contained in this document does not fulfil or replace any individual's or Member's legal, regulatory or other duties or obligations in respect of their operations. Individuals and Members remain solely responsible for the safe, lawful and proper conduct of their operations.
Share your safety incidents with IMCA online. Sign-up to receive Safety Flashes straight to your email.