Lifting operations: Wire hoist rope failure
- Safety Flash
- Published on 28 April 2020
- Generated on 3 September 2025
- IMCA SF 14/20
- 2 minute read
Jump to:
What happened?
When conducting a standard lifting operation of a 24.5te storage vessel and lifting frame (approximately 36% of the crane 70te maximum rated capacity) the wire hoist rope (WHR) failed causing the load, main block and length of wire to drop approximately 3 m to the wharf. No personnel were injured.
The maintenance, inspection, and testing regime applied to the WHR was consistent with general industry practice, guidelines, and company requirements and included third-party examination and certification. However, localised internal corrosion of the wire hoist rope (WHR) went undetected.
The metallurgical examination conducted on the wire hoist rope after the incident concluded that the wire hoist rope failed by a ductile overload mechanism following corrosion damage during service, particularly of the core wires. The lack of protective zinc galvanised coating on the wire hoist rope was a significant contributor to the eventual failure.
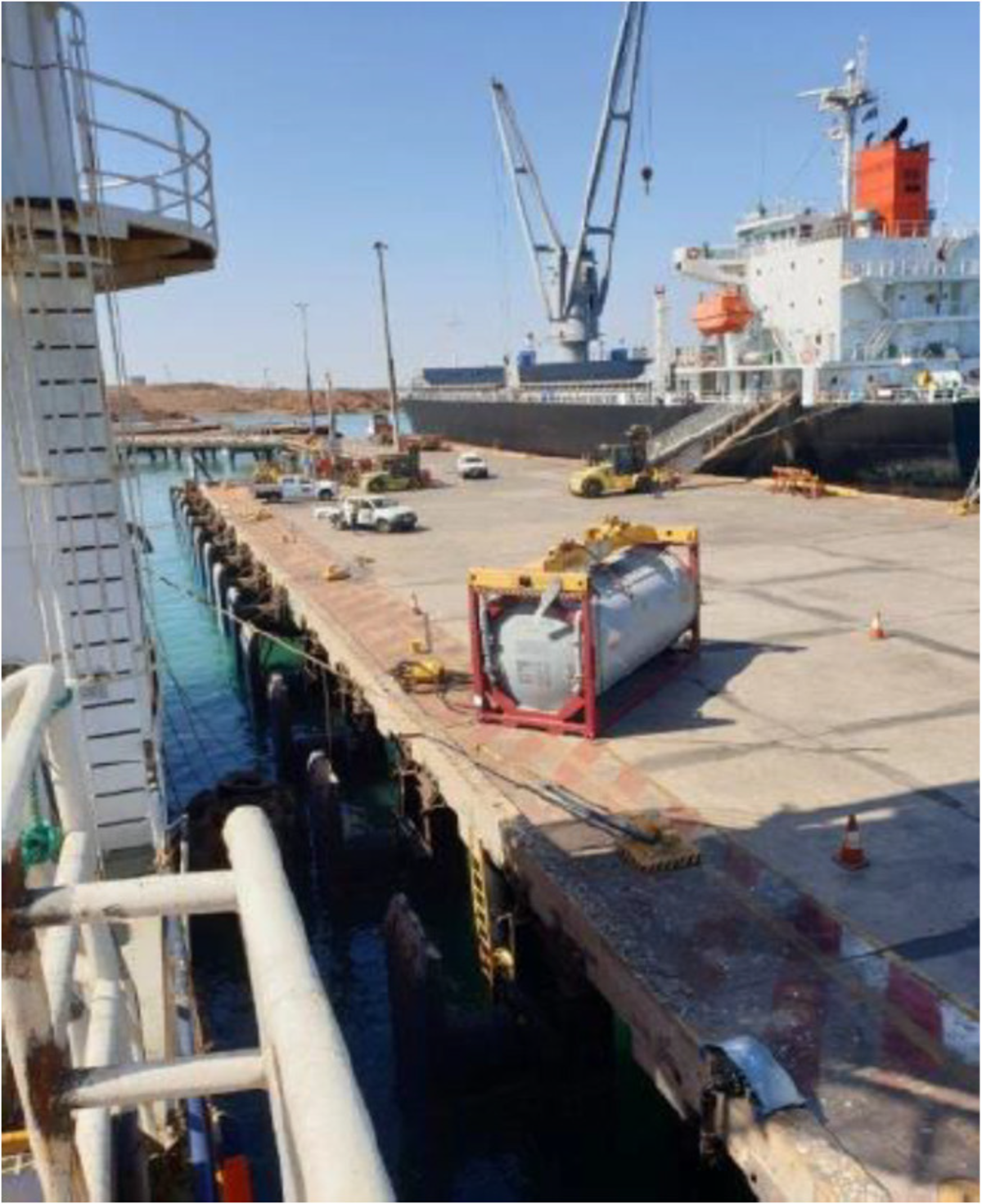
What lessons were learned?
- Reliance on ‘industry practice and guidelines’ alone when maintaining, testing and inspecting wire hoist ropes may not be sufficient. Frequency of use, intended loads, environmental conditions, time in service, and criticality of the wire hoist rope should be specifically considered.
- Implement crane wire maintenance regimes for specific individual wire rope types using original equipment manufacturer input coupled together with a competent person’s assessment of the risks, giving due regard for the operating environment and intended use of the crane/wire rope.
- Establish criteria to determine when and how magnetic wire rope (MRT) testing should be applied (frequency, triggers, length of wire).
Members may wish to refer to:
- Guidance on wire rope integrity management for vessels in the offshore industry (IMCA LR001, IMCA HSS022, IMCA M194)
Related Safety Flashes
-
IMCA SF 04/18
20 February 2018
-
-
IMCA SF 22/15
15 December 2015
-
IMCA SF 21/15
7 December 2015
IMCA Safety Flashes summarise key safety matters and incidents, allowing lessons to be more easily learnt for the benefit of the entire offshore industry.
The effectiveness of the IMCA Safety Flash system depends on the industry sharing information and so avoiding repeat incidents. Incidents are classified according to IOGP's Life Saving Rules.
All information is anonymised or sanitised, as appropriate, and warnings for graphic content included where possible.
IMCA makes every effort to ensure both the accuracy and reliability of the information shared, but is not be liable for any guidance and/or recommendation and/or statement herein contained.
The information contained in this document does not fulfil or replace any individual's or Member's legal, regulatory or other duties or obligations in respect of their operations. Individuals and Members remain solely responsible for the safe, lawful and proper conduct of their operations.
Share your safety incidents with IMCA online. Sign-up to receive Safety Flashes straight to your email.