Near-miss: Corrosion caused crane boom failure during heavy lifting
- Safety Flash
- Published on 7 December 2015
- Generated on 2 July 2025
- IMCA SF 21/15
- 3 minute read
Jump to:
A member has reported an incident in which a crane boom failed under load while lifting a 37T load.
What happened?
The incident occurred after the load was taken up by the wire. The operator then attempted to boom up in preparation to swing the load from the jetty to the vessel. Almost immediately on booming up, the operator heard a loud bang and the load dropped approximately 30 cm.
On investigation, it was found that the boom had buckled and cracked. The load was de-rigged safely; there were no injuries, nor was there any secondary damage to the load being lifted, or to the vessel.
What were the causes?
On investigation, it was found that the boom had buckled and cracked. The load was de-rigged safely; there were no injuries, nor was there any secondary damage to the load being lifted, or to the vessel.
The crane boom was disassembled and an investigation was carried out. Our member noted the following:
- A large crack along the welded boom section was discovered which appeared to be old fatigue cracking and internal corrosion of the boom which evolved into a catastrophic materials failure.
- The crane had undergone recent testing by a third party, which did not discover the cracking.
- Testing/certification of the crane did not include Non-Destructive Examination (NDE) of critical areas.
- Several management failings were reported but none of these directly contributed to the incident.
The main cause of the incident was found to be material failure.
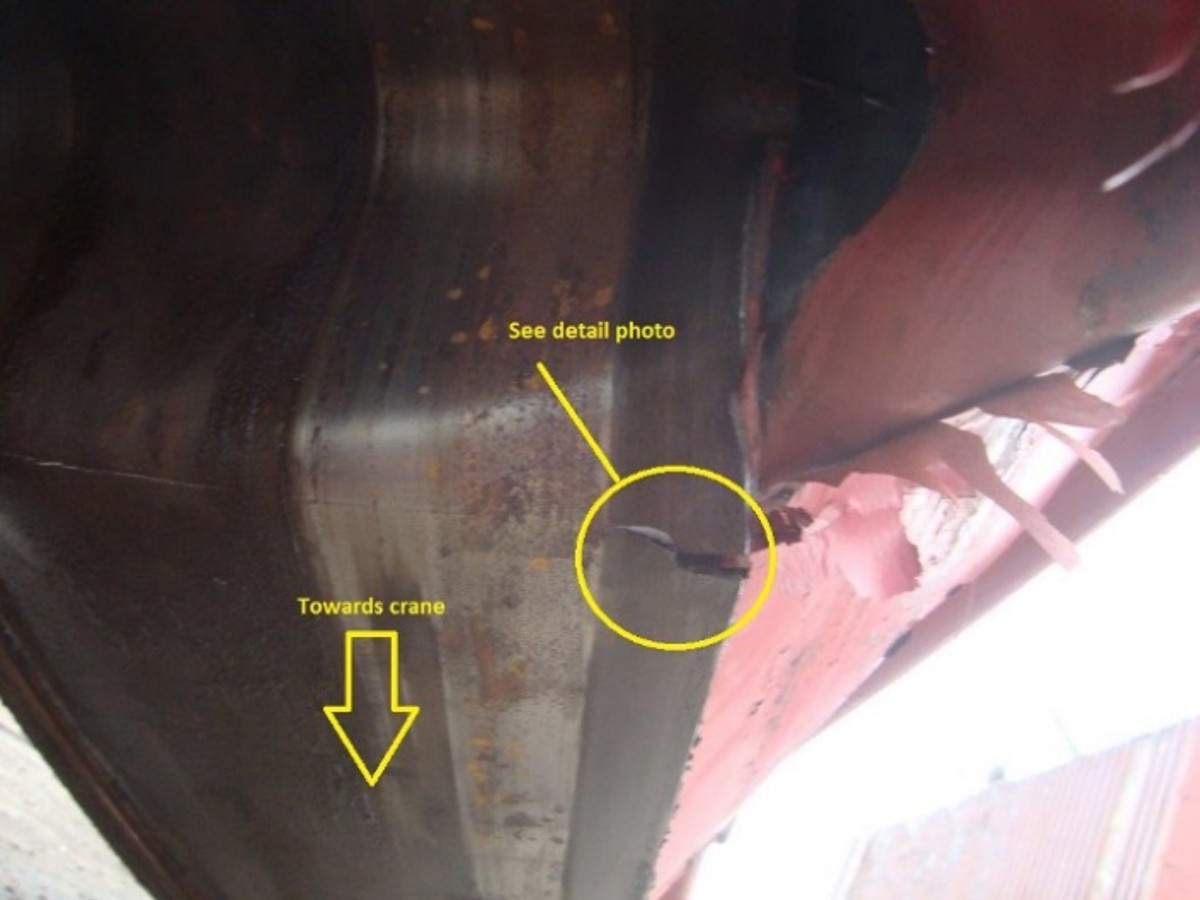
dynamic fracture caused by loss of material integrity
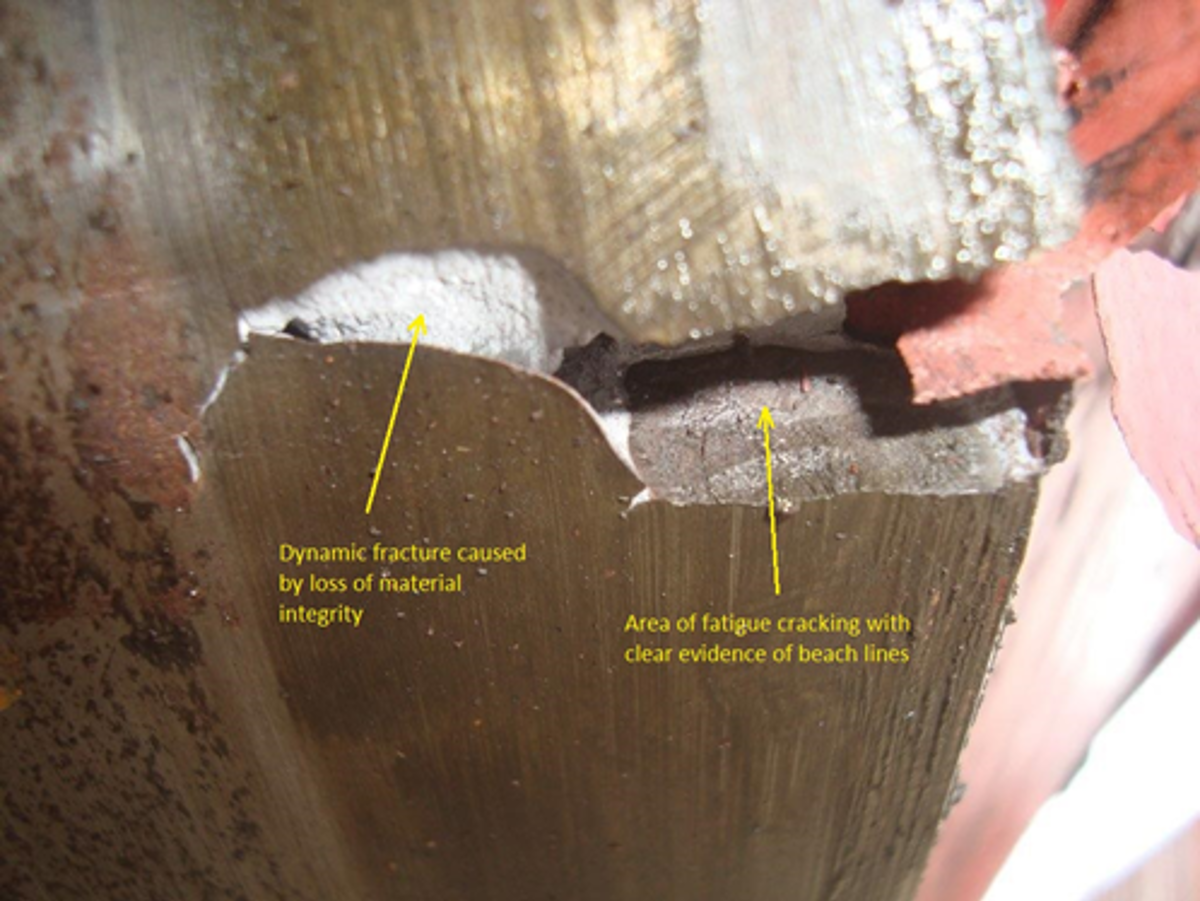
area of fatigue cracking with clear evidence of beach lines
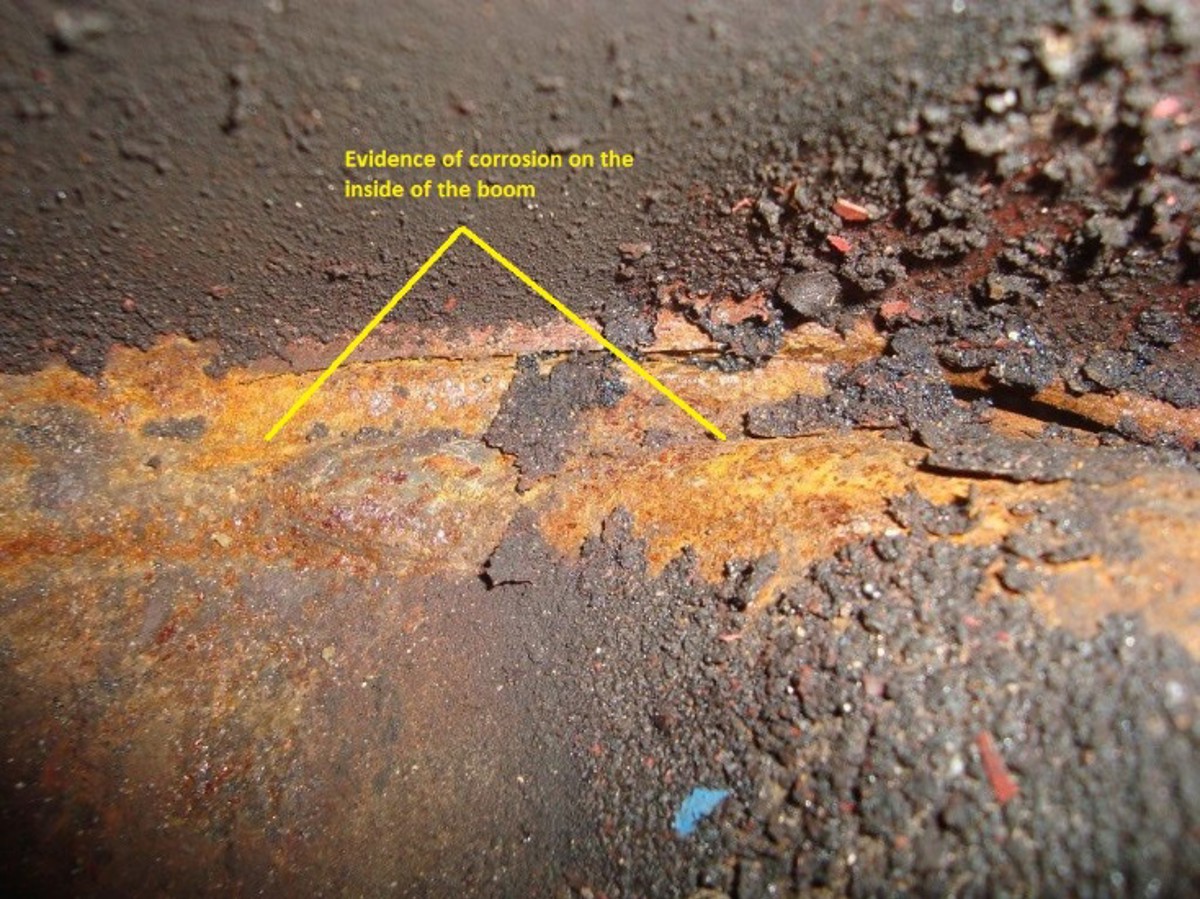
close-up of corrosion
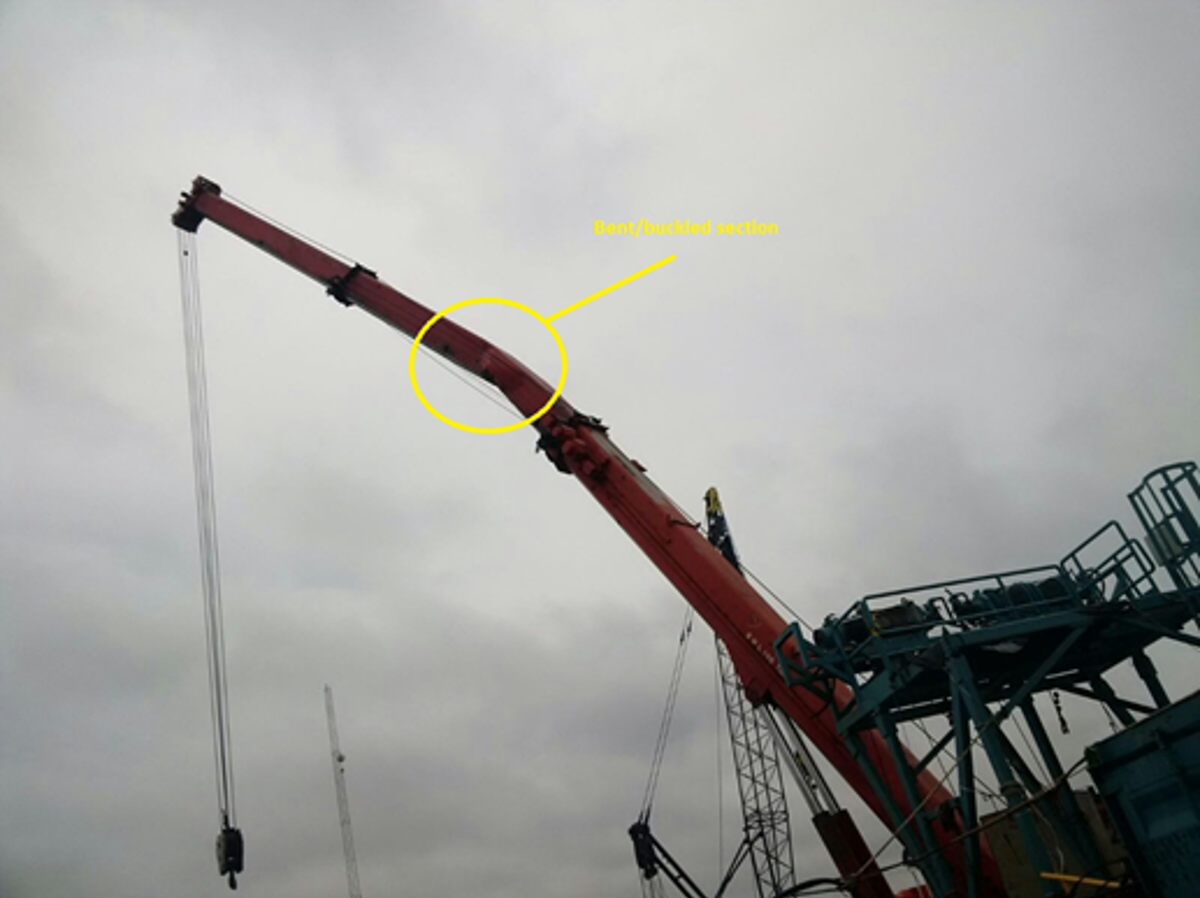
point at which crane boom buckled (marked)
Lessons learnt
The lessons learnt were:
- Lifting procedure was good and allowed accommodation of an unforeseen catastrophic failure.
- Because the operator kept the load as low as possible and no one was in the path of the load there were no injuries or damage beyond the crane itself.
- A more thorough NDE planned maintenance/inspection plan should be drawn up for this type of lifting device to include a spot check Magnetic Particle Inspection (MPI) or similar after-load testing of critical stressed areas -perhaps including life span of critical components.
Actions
Our member took the following actions:
- Reviewed the crane planned maintenance system.
- Researched capability and cost of NDE to determine an appropriate amount of inspection versus risk.
In this case, to draw members’ attention to failures of equipment in general (13% of all incidents), crane incidents (5% of all incidents), or to incidents including the words ‘boom’ (6 incidents) or ‘corrosion’ (4 incidents) may not add any real value.
Related safety flashes
-
IMCA SF 11/08
23 June 2008
IMCA Safety Flashes summarise key safety matters and incidents, allowing lessons to be more easily learnt for the benefit of the entire offshore industry.
The effectiveness of the IMCA Safety Flash system depends on the industry sharing information and so avoiding repeat incidents. Incidents are classified according to IOGP's Life Saving Rules.
All information is anonymised or sanitised, as appropriate, and warnings for graphic content included where possible.
IMCA makes every effort to ensure both the accuracy and reliability of the information shared, but is not be liable for any guidance and/or recommendation and/or statement herein contained.
The information contained in this document does not fulfil or replace any individual's or Member's legal, regulatory or other duties or obligations in respect of their operations. Individuals and Members remain solely responsible for the safe, lawful and proper conduct of their operations.
Share your safety incidents with IMCA online. Sign-up to receive Safety Flashes straight to your email.