BSEE: Lack of training with hydraulic torque wrench contributes to fatality
- Safety Flash
- Published on 1 July 2023
- Generated on 24 August 2025
- IMCA SF 16/23
- 3 minute read
Jump to:
The United States Bureau of Safety and Environmental Enforcement (BSEE) has published Safety Alert 459 relating to a fatality which occurred on a drillship in the Gulf of Mexico.
What happened?
While unlatching the lower Marine Riser Package from the Blowout Preventer in preparation for ship relocation, a crew member was lifted into the air after being struck by a hydraulic torque wrench (HTW), hitting a riser clamp approximately six feet above the elevated work deck before falling to the rig floor.
The crew member was given first aid and transported to the drillship’s hospital, where he was later pronounced deceased.
The incident investigation found that the rig crew was using a hydraulic torque wrench to extract the bolts from a telescopic riser joint (TJ) flange.
During the operation, the HTW T socket became stuck between the bolt head and the tapered edge of the TJ. After failing to manually dislodge the HTW using physical exertion, the rig crew utilised a hydraulic utility wrench (HUW) to supply upward force and applied tension to free the tool.
After applying the upward force, the torque wrench became unstuck under tension and shot upwards leading to the crew member being struck.
What went wrong?
- The risk that the hydraulic torque wrench would get stuck on the TJ bevelled edge, was not recognised.
- There was no comprehensive understanding of the Task Risk Assessments associated with the riser pull.
- There was a failure to effectively communicate all learnings from the previous riser pulls.
- There was a lack of formalised training for the use of these hydraulic tools.
- The design of both tools was not optimal and may have contributed to the incident.
- Contributing causes:
- Failure to initiate Stop Work Authority.
- Discrepancies in roles and responsibilities for the Drill Floor Observer (a supervisor).
- Failure to initiate Stop Work Authority.
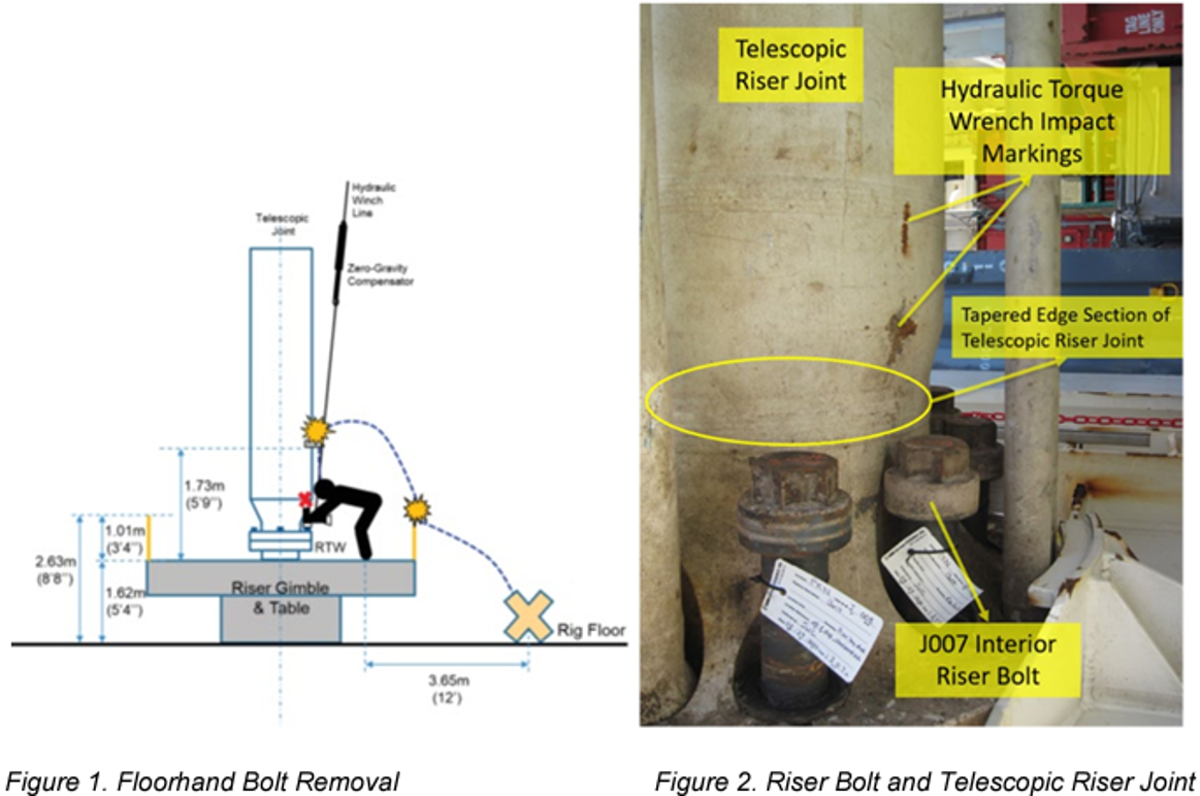
Actions
- Ensure Job Safety Analysis captures the limitations of the tools in use.
- Verify that all employees understand the Job Safety Analysis and have been formally trained on operating hydraulic or other power-driven tools.
- Emphasise the initiation of Stop Work Authority if an imminent danger is observed.
- Ensure supervisors and managers understand their responsibilities to monitor all aspects of jobs occurring in the areas over which they have control.
- Use tools that are compatible with, and specifically designed for use in, the particular work environment.
- Could a load indicator, or a similar design mechanism, be of use on such hydraulic wrench tools?
Related safety flashes
-
IMCA SF 10/23
20 April 2023
-
-
IMCA SF 21/22
26 September 2022
-
IMCA SF 09/20
31 March 2020
-
IMCA Safety Flashes summarise key safety matters and incidents, allowing lessons to be more easily learnt for the benefit of the entire offshore industry.
The effectiveness of the IMCA Safety Flash system depends on the industry sharing information and so avoiding repeat incidents. Incidents are classified according to IOGP's Life Saving Rules.
All information is anonymised or sanitised, as appropriate, and warnings for graphic content included where possible.
IMCA makes every effort to ensure both the accuracy and reliability of the information shared, but is not be liable for any guidance and/or recommendation and/or statement herein contained.
The information contained in this document does not fulfil or replace any individual's or Member's legal, regulatory or other duties or obligations in respect of their operations. Individuals and Members remain solely responsible for the safe, lawful and proper conduct of their operations.
Share your safety incidents with IMCA online. Sign-up to receive Safety Flashes straight to your email.