First aid injury: Contact with spinning spooler arm
- Safety Flash
- Published on 18 January 2013
- Generated on 16 August 2025
- IMCA SF 01/13
- 3 minute read
Jump to:
A Member has reported an incident in which a spinning handle on a spooler arm hit someone on the upper arm, wrist and knuckles, causing light bruising.
What happened?
The incident occurred when a hydraulic grapple (complete with 12m section of 20″ pipe) was being recovered to deck using the vessel’s crane whip line. A third party technician, who was operating the hydraulics at the powered reeler, was paying in on the hydraulic hoses, and using the manual handle on the spooler arm to evenly wrap the hoses on the drum.
As the grapple was being lifted inboard the vessel took a heave, which pulled the hoses tight causing the handle on the spooler arm to spin round. As the handle spun it caught the third party technician on the upper arm, wrist and knuckles. The technician was wearing full personal protective equipment (PPE) at the time but was taken to the medic, where he was checked over and found to have light bruising.
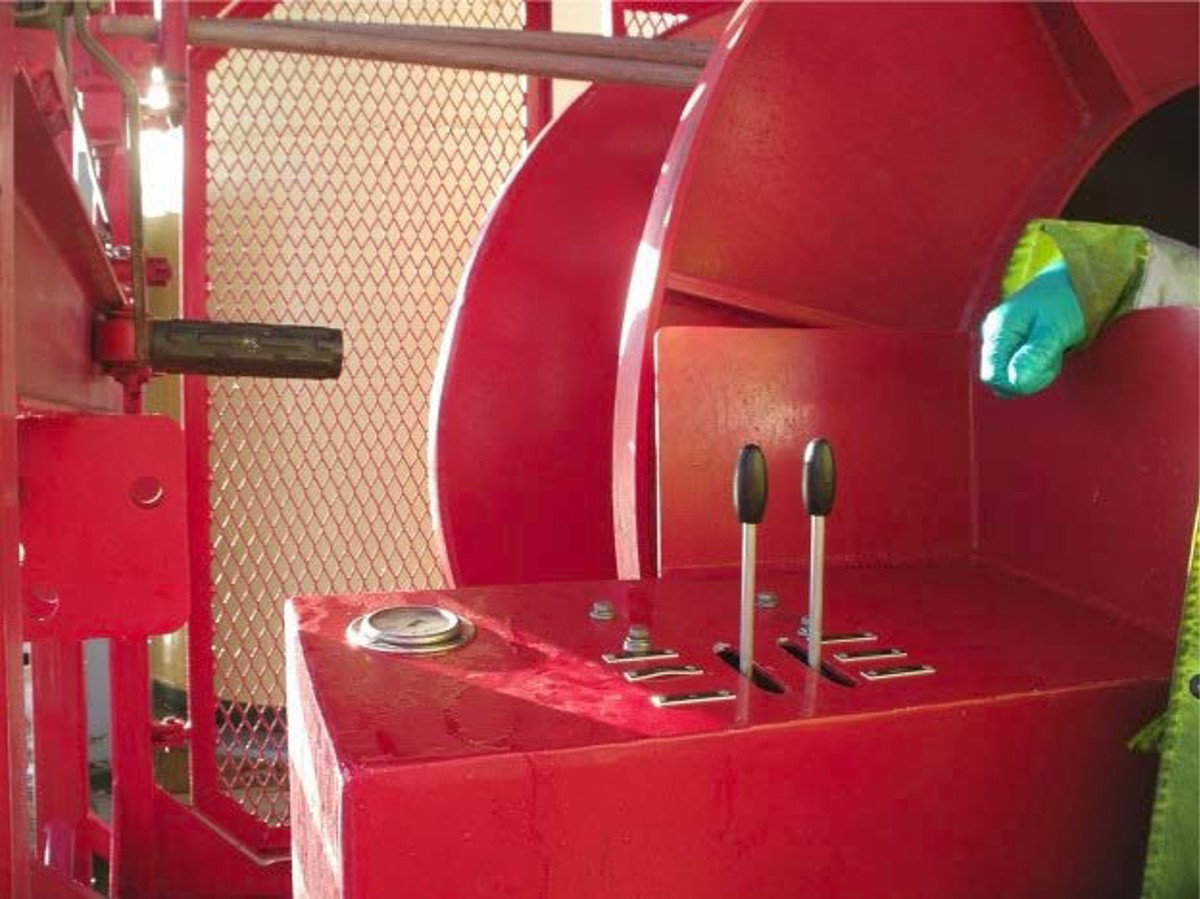
spooler arm and hydraulic spooler controls where injured person was standing
What were the causes?
An investigation revealed the following root causes:
- The vessel experienced a heave while the hydraulic hoses were being manually spooled/wrapped around a drum during grapple/pipe recovery operations.
- Insufficient slack left on the hydraulic hoses to accommodate the conditions/heave being experienced by the vessel led to the hoses becoming tight and the spooler arm handle to spin.
- Lack of recognition of a potential hazard (the spooler arm handle spinning if the hoses went tight) was such that there was no recognition of the need to ensure that sufficient slack was left on the hoses to avoid the handle spinning, or that body position during grapple recovery operations (if too close to the spooler arm handle) could potentially result in contact with it.
- The design/layout of the work area and location of equipment allows for hand/body positioning to get close enough to the spooler arm handle to make contact with it, in particular during times when vessel was experiencing a heave.
- A toolbox talk/pre-task assessment was carried out with the third party personnel in attendance; however it appears to have focused mainly on lifting/rigging operations hazards and escape routes should problems arise during lifting operations, but not potential vessel heave in moderate sea states, subsequent hydraulic hoses tightening and workspace issues that could result in contact with the protruding spooler arm handle on recovery of the grapple.
- The initial revision of the job safety and environmental analysis for the grapple operations did not include the potential hazard/risks associated with tightening of hoses and safe body positioning for returning/lifting the grapple to deck or debris pile job step. In addition the necessary control measure of ensuring that the operators stand clear of the spooler arm handle and/or ensuring that the handle is locked was not included.
Lessons learnt
The following lessons were learnt:
- Use of an automatic spooler would prevent the need for hand/body positioning so close to the spooler arm handle during recovery of the grapple.
- In addition to ergonomic issues, it was found that personnel were exposed to environmental hazards, i.e. the weather, when operating the controls. Adapting this area to include some form of habitat would mean operators were protected from the weather.
Additionally, a formal change was made to the launch and recovery operations process/tasked-based risk assessment.
IMCA Safety Flashes summarise key safety matters and incidents, allowing lessons to be more easily learnt for the benefit of the entire offshore industry.
The effectiveness of the IMCA Safety Flash system depends on the industry sharing information and so avoiding repeat incidents. Incidents are classified according to IOGP's Life Saving Rules.
All information is anonymised or sanitised, as appropriate, and warnings for graphic content included where possible.
IMCA makes every effort to ensure both the accuracy and reliability of the information shared, but is not be liable for any guidance and/or recommendation and/or statement herein contained.
The information contained in this document does not fulfil or replace any individual's or Member's legal, regulatory or other duties or obligations in respect of their operations. Individuals and Members remain solely responsible for the safe, lawful and proper conduct of their operations.
Share your safety incidents with IMCA online. Sign-up to receive Safety Flashes straight to your email.