Main crane hoist wire damage
- Safety Flash
- Published on 10 November 2020
- Generated on 3 July 2025
- IMCA SF 31/20
- 3 minute read
Jump to:
What happened?
A 70-centimetre length of main crane hoist wire was found to be damaged during an inspection.
During pile installation operations, small plastic items were observed to be attached to the 400te crane main wire.
The plastic was identified as ducting, a protection barrier from water/grease spray when recovering or paying out the crane wire within the crane pedestal.
After internal consultation with both company technical specialists and the offshore management team, it was decided to cut 1,410 metres of wire rope from the hook subsea using an ROV. The crane wire re-socketing was then performed onboard the vessel main deck. This work cost 71 hours of downtime.
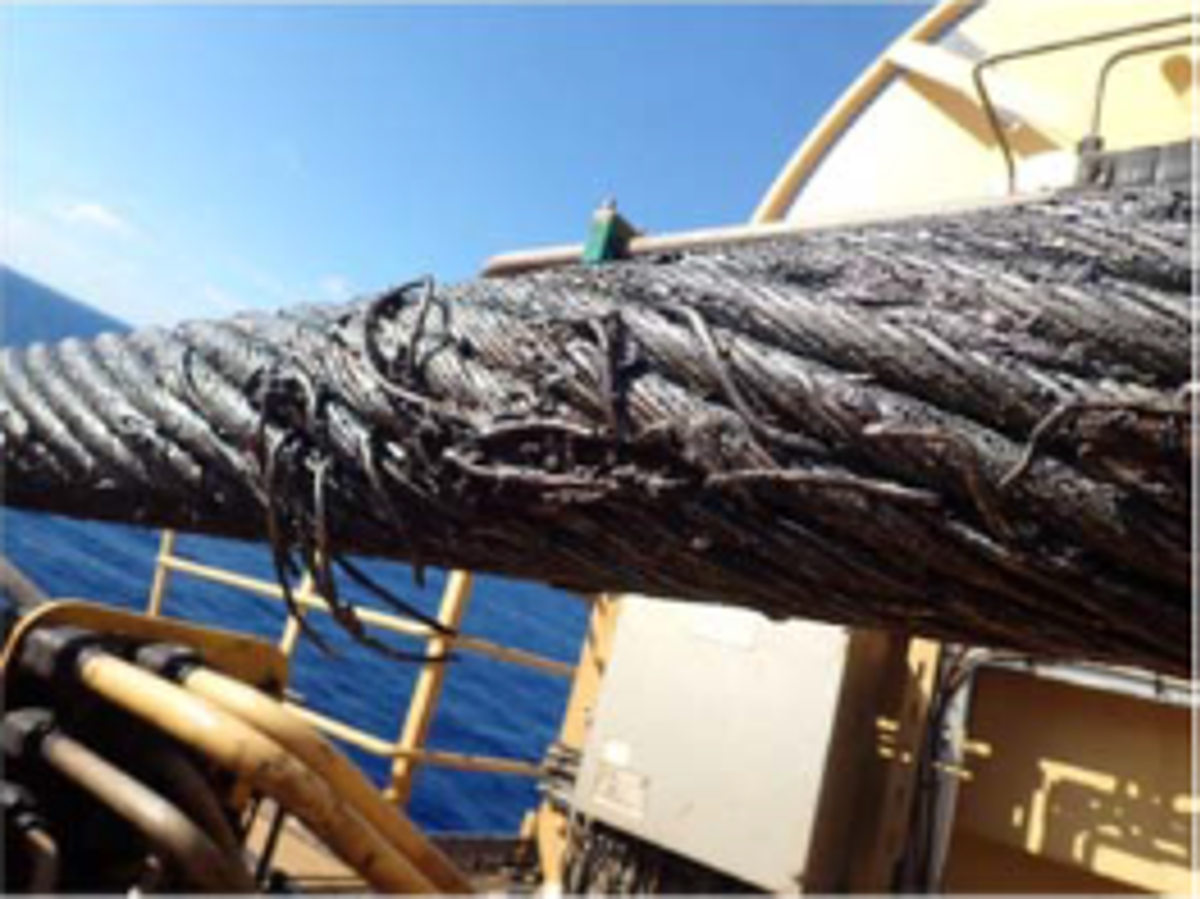
Findings
- A contact/rubbing point was identified on the knuckle aperture where the crane wire passed through the knuckle boom.
- The crane operator struggled to engage the Active Heave Compensation (AHC) and proceeded to disengage the auto knuckle function to activate AHC.
- The crane operator ignored the angle deviation alarm and did not notify the lay technician of any issues;
- The resultant knuckle position extended beyond the working parameters of the special lift mode which caused the crane wire to contact the knuckle aperture. When AHC was activated, it created a sawing motion against the inner side of the aperture which over a period of lifting operations damaged the wire rope and cut a groove into the aperture structure.
- The event occurred 3 days before the plastic was observed on the wire.
- The crane manufacturer was not able to provide crane familiarisation to the crane operator onboard the vessel due to COVID-19 travel restrictions. The company crane operator familiarisation checklist was completed onboard.
- The crane operator had knuckle boom experience and possessed a crane trainer/assessor qualification.
- At the time of the incident, the crane operating system displayed a KN-Boom Auto virtual button with no other information when selected. The crane manufacturer subsequently recommended to upgrade the system to enable a pop-up screen showing the limits in special lift mode when the KN-Boom Auto virtual button is selected.
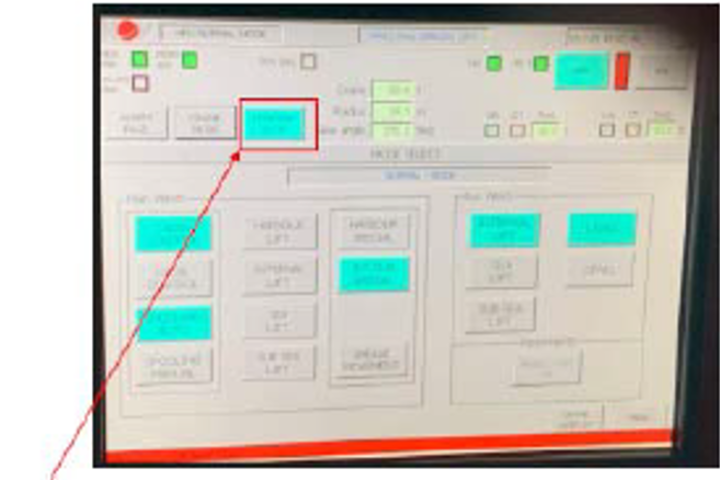
Photograph 1 shows the system configuration at the time of the incident, which displayed the KN-Boom Auto virtual button with no other information
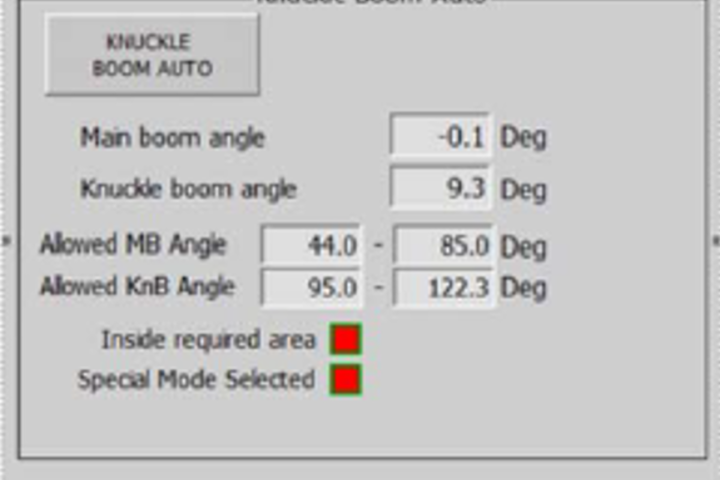
Photograph 2 shows an example of a pop-up screen with the limits displayed when the KN-Boom Auto virtual button is selected
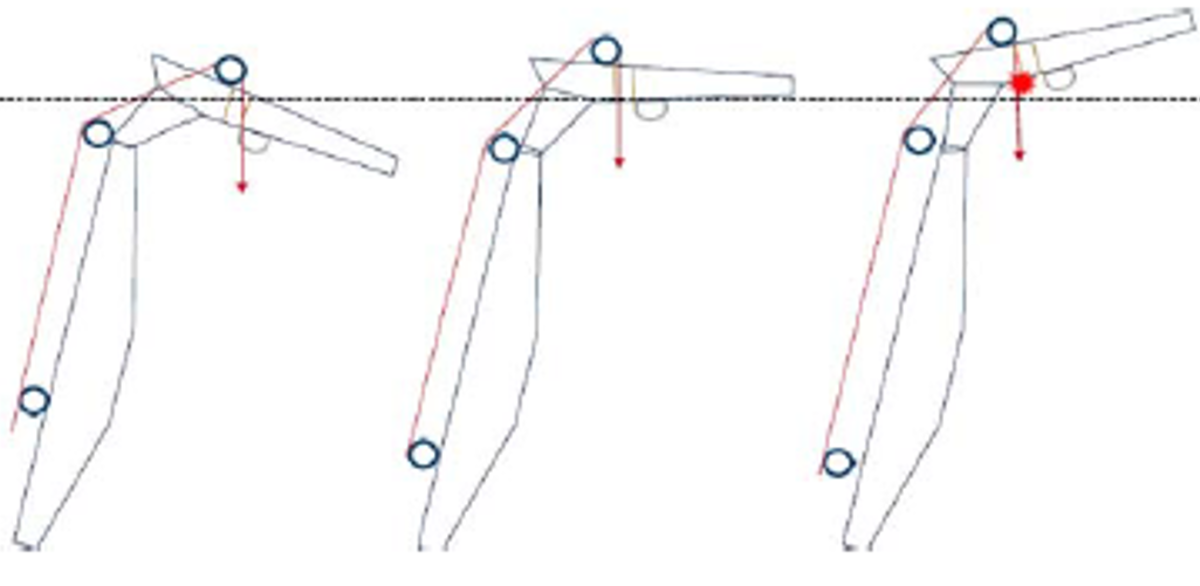
Actions taken? Lessons learned?
-
Reinforce to equipment operators the importance of always adhering to equipment manufacturer’s instructions and raising any issues that are experienced.
-
Review similar equipment to verify whether operating systems can be improved to optimise the human/machine interface.
Related Safety Flashes
-
IMCA SF 11/08
23 June 2008
-
IMCA SF 10/05
31 October 2005
-
IMCA SF 03/98
1 May 1998
IMCA Safety Flashes summarise key safety matters and incidents, allowing lessons to be more easily learnt for the benefit of the entire offshore industry.
The effectiveness of the IMCA Safety Flash system depends on the industry sharing information and so avoiding repeat incidents. Incidents are classified according to IOGP's Life Saving Rules.
All information is anonymised or sanitised, as appropriate, and warnings for graphic content included where possible.
IMCA makes every effort to ensure both the accuracy and reliability of the information shared, but is not be liable for any guidance and/or recommendation and/or statement herein contained.
The information contained in this document does not fulfil or replace any individual's or Member's legal, regulatory or other duties or obligations in respect of their operations. Individuals and Members remain solely responsible for the safe, lawful and proper conduct of their operations.
Share your safety incidents with IMCA online. Sign-up to receive Safety Flashes straight to your email.