LTI: Hand injury during capstan maintenance
- Safety Flash
- Published on 3 July 2025
- Generated on 18 August 2025
- IMCA SF 12/25
- 3 minute read
Jump to:
A crew member was injured when their hand was trapped between a wire clamp on the underside of the capstan and the deck.
What happened?
A crew member was injured when their hand was trapped between a wire clamp on the underside of the capstan (where the greasing point was located) and the deck. The incident occurred during capstan maintenance, when the crew member and an officer were greasing the capstan. The crew member signalled the officer to engage the capstan, the unit started turning, and the crew member got his hand trapped, causing a serious injury which required medical assistance. The crew member was subsequently taken ashore to hospital for further treatment.
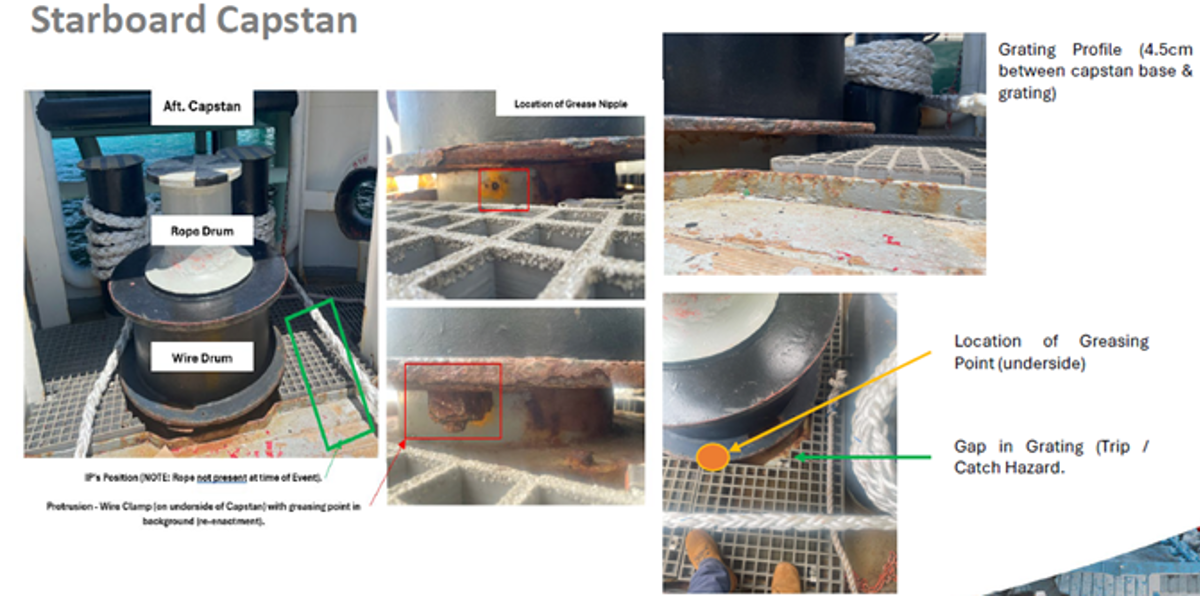
What went wrong?
Access to the greasing point on the underside of capstan was very difficult and it could not easily be seen. As a result it was not spotted that there was a bracket (which caught the hand when the capstan was rotated).
What were the causes
- Even following “risk-based thinking”, a toolbox talk and discussion of the task beforehand, someone’s hand still went into the line of fire.
- Poor design
̶ Access to the greasing point required a worker to lie on their back on deck. Consideration had not been given to a more ergonomic design.
̶ The design of the grease gun itself made it necessary for a worker to put their hand in an enclosed area, and encouraged removal of gloves to allow the worker to use fingers to “feel” for the greasing point. - That there was a wire clamp on the rotating underside of the capstan had not been identified in the risk assessment – it was very difficult to see.
Actions taken
- Modifications were made to the areas near the vessel capstans, including removable fibre-glass grating, removal of the wire clamp on the underside of the capstan.
- Modifications were made to grease points to enable better access (extension pieces were fitted to the grease points which alleviated the need for hands to be underneath the unit).
- Procedures for deck maintenance were revised to provide clearer and more explicit instructions, particularly for rotating machinery and where there are potential “line of fire” issues.
- A thorough vessel-wide and fleet-wide inspection of potential “line of fire” hazards took place.
Lessons learned
- Our members’ vessels have multiple pieces of often very similar equipment – engines, generators, cranes, winches, capstans etc. Are there unnoticed inconsistencies or differences between similar equipment or even indeed between similar vessels, which might hinder safe operations?
- In reviewing the risk of “line of fire” hand injuries, could other unrelated safety risks be revealed? Be open to this possibility. In this case, our member found that near one capstan there was an unnoticed risk of a foot getting caught.
- A blend of both system and design factors have collectively contributed to a single decision (i.e. a rotating capstan whilst a hand is in the line of fire) to result in an injury.
Related Safety Flashes
-
IMCA SF 22/23
12 September 2023
-
-
IMCA SF 04/21
2 February 2021
-
-
IMCA SF 22/22
3 October 2022
-
-
IMCA SF 16/24
14 August 2024
-
IMCA Safety Flashes summarise key safety matters and incidents, allowing lessons to be more easily learnt for the benefit of the entire offshore industry.
The effectiveness of the IMCA Safety Flash system depends on the industry sharing information and so avoiding repeat incidents. Incidents are classified according to IOGP's Life Saving Rules.
All information is anonymised or sanitised, as appropriate, and warnings for graphic content included where possible.
IMCA makes every effort to ensure both the accuracy and reliability of the information shared, but is not be liable for any guidance and/or recommendation and/or statement herein contained.
The information contained in this document does not fulfil or replace any individual's or Member's legal, regulatory or other duties or obligations in respect of their operations. Individuals and Members remain solely responsible for the safe, lawful and proper conduct of their operations.
Share your safety incidents with IMCA online. Sign-up to receive Safety Flashes straight to your email.