- Discover how we are helping Members reduce emissions: Explore the ProjectGHG hub now.
- Join the global DP Community at the IMCA DP Conference in Amsterdam. 21 and 22 May. Book now
- Register your interest for the IMCA Global Summit 2024. 3-4 December, Utrecht, Netherlands.
- Now booking. Underwater Ship Husbandry Seminar. 10 October 2024, Singapore.
Near-miss: Diver working under suspended load
A member has reported an incident in which a diver found himself working under a suspended load.
Whilst conducting diving operations around a subsea manifold, a subsea work basket weighing 375kg in water was landed without proper warning very close to a diver standing on the subsea manifold. Tools and equipment were being deployed to the divers using a cherry picker crane without heave compensation. Part of the lift planning was a ‘short mark’ established prior to subsea deployment of the load. The length of winch wire deployed was then closely monitored on the crane line out meter to ensure that loads were stopped at a safe distance from the divers working on the seabed. Additionally, the crane wire had a transponder attached which allowed the depth to be monitored by the dive control department. Once the load was at the required short mark it was standard practice to have the remotely operated vehicle (ROV), in conjunction with a diver, spot the load and then monitor the final stage of the deployment to the seabed.
Dive control had requested that tools and equipment be deployed using a 1m x 1m work basket. The basket was prepared with a beacon, strobe and light sticks attached to help improve its visibility subsea. On previous dives the short mark had been set at 95m with a working depth of 108m but, as the divers were having difficulty seeing the loads due to poor visibility, the short mark was altered to 100m to allow the load closer and make it easier to spot. The work basket was deployed and the line out meter zeroed at the splash zone to ensure the load could be stopped at the required mark.
Dive control requested that diver 1 make his way to the top of the manifold to prepare for the basket being landed. When he arrived at the manifold he could not see the load and was told it was on its way down. While he was waiting for the load to arrive he started to inspect the landing zone to ensure it was clear to land the work basket. As he was doing so, the deployed work basket suddenly landed behind him on top of the manifold.
Diver 1 called an immediate ‘all stop!’ and at the same time the crane driver informed dive control that as per his line out
meter he had reached the required short mark. During this operation the ROV had not been requested to spot the load at any point during the deployment.
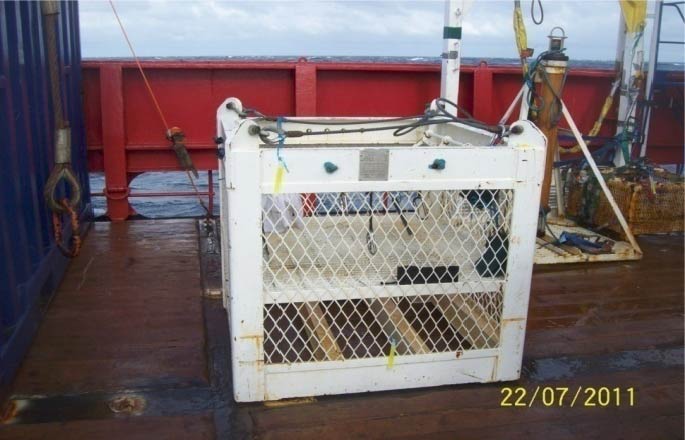
An investigation was conducted, noting the following:
- There was no written and agreed procedure for this operation with lifts being completed using usual practice;
- There had been no risk assessment for deploying subsea loads from the crane;
- There was no lift plan in place for the work basket and hence no discussion of the work basket during toolbox talks, which might have highlighted potential hazards and considerations for personnel involved;
- Though trained in using the picker crane, the crew using it may not have been fully aware that movement of the boom and knuckle could result in the load being at a different position with no change on the line out meter reading;
- The crane crew may not have closely monitored the reading from the transponder and instead used the line out meter reading as the primary source of monitoring the depth of the load;
- Several previous faults had been reported on the crane line out meter with the meter returning to zero during subsea operations; these reports had been investigated but no permanent fault had been identified;
- Diver 1 should have been informed to inspect the landing zone for the work basket prior to the load being deployed overboard and then instructed to move out of the landing zone until the load had reached the short mark and was being monitored by dive control using the ROV. In this way, he would have been protected from working underneath a suspended load.
The following actions were taken:
- Develop and circulate vessel-specific procedures for deployment of loads with picker cranes or winches, including safe over-boarding areas, communication protocols and illustration of roles and responsibilities of departments;
- Develop specific lift plans for all working baskets and equipment in use subsea, including reference to any job risk assessment (JRA) where divers or ROVs are present subsea;
- Ensure all personnel operating picker cranes or winches have completed a suitable level of competency training for that piece of equipment.
Safety Event
Published: 1 November 2011
Download: IMCA SF 12/11
IMCA Safety Flashes
Submit a Report
IMCA Safety Flashes summarise key safety matters and incidents, allowing lessons to be more easily learnt for the benefit of all. The effectiveness of the IMCA Safety Flash system depends on Members sharing information and so avoiding repeat incidents. Please consider adding [email protected] to your internal distribution list for safety alerts or manually submitting information on incidents you consider may be relevant. All information is anonymised or sanitised, as appropriate.
IMCA’s store terms and conditions (https://www.imca-int.com/legal-notices/terms/) apply to all downloads from IMCA’s website, including this document.
IMCA makes every effort to ensure the accuracy and reliability of the data contained in the documents it publishes, but IMCA shall not be liable for any guidance and/or recommendation and/or statement herein contained. The information contained in this document does not fulfil or replace any individual’s or Member's legal, regulatory or other duties or obligations in respect of their operations. Individuals and Members remain solely responsible for the safe, lawful and proper conduct of their operations.